Advanced 3D metrology for car body

GOM has worked on improving the speed and accuracy of its latest generation of optical 3D coordinate measuring machines
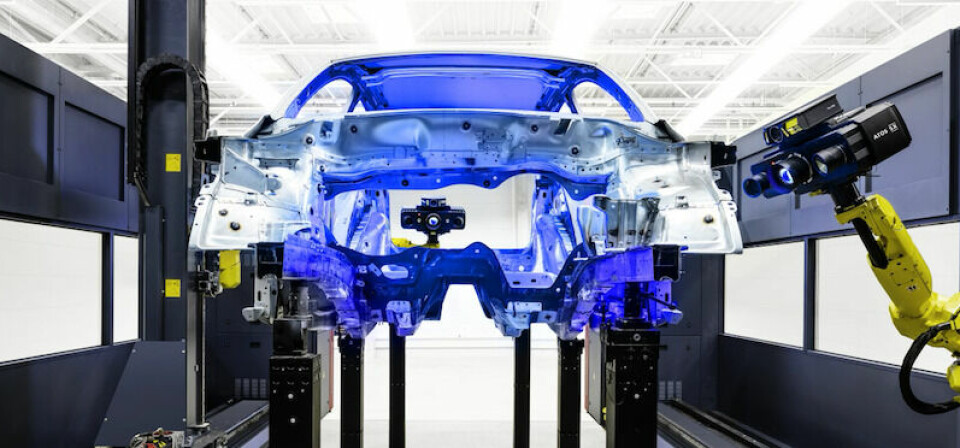
The automotive industry has undergone many changes over recent years, and new technologies are influencing production processes with the aim of making manufacturing more efficient. The implementation of robotics on the assembly line is among the best-known examples of this ongoing development. Also, in industrial metrology, there are new technologies that lead to faster and more efficient processes. The automotive sector benefits particularly from this.
The special demand in the field of automotive metrology is to ensure high quality standards and to operate as fast as volume sellers require. The challenges facing the entire sheet metal forming industry today can be clearly seen in the automotive body construction – the area with the highest demands on part strength, safety and design. Design lines and narrow gap sizes are specifically used to convey a sense of quality and serve as an indication for high-precision and demanding manufacturing processes.
To meet these requirements, the automotive industry and, consequently, the entire sheet metal forming industry, relies on 3D metrology and 3D testing within the entire manufacturing process chain. Optical 3D coordinate measuring machines capture more detailed and digestible quality information about an object in significantly shorter measuring times than traditional coordinate-measuring machines (CMMs). A significant advantage of optical metrology is the full-field evaluation and visualisation in colour-coded deviation plots. This way, problematic areas of parts can be identified intuitively and respective measures can be derived. Measuring times should be as fast as possible, and measured data should be available in real time to ensure very short response times.
GOM has worked on precisely these two criteria – speed and accuracy – and now presents its latest sensor generation. Fast measurement times and precise data quality are the buzzwords of the new 3D scanners. Five technology leaps were made before the latest ATOS sensors were developed, with process acceleration and increased reliability being paramount for the latest systems for all metrological applications.
The Fifth Generation: ATOS 5 | ATOS 5XATOS 5 and ATOS 5X are two new high-speed sensors of the ATOS family. The robust sensors are fast and precise. The Blue Light Equalizer is a component that was especially developed to provide an ultra-powerful light source that enables the use of large measuring volumes.
The bright light source of the ATOS 5 is based on blue LED light. ATOS 5X uses the integrated Laser Light Compressor to generate ultra-bright light. This allows for the measuring areas of up to 1,000mm while at the same time resulting in extremely short exposure times. As a result, both measuring systems achieve high-precision data in a short measuring time. The GOM data quality is particularly evident in the detail sharpness of the 3D models, for example, in the precise display of smallest details, rib structures, narrow radii and hemmed edges.
The enhanced measuring areas combined with high resolution results in faster processes due to fewer measurements. At the same time, fixture design can be simplified as a larger surface is captured and fewer reference points are required. During the measuring procedure, acquisition times of 0.2 seconds are reached.
Thanks to the interference-free data transfer via fiber optic cables, the independence of the surrounding system environment and the sensor-controlled monitoring of the calibration status, the systems can be used in production.
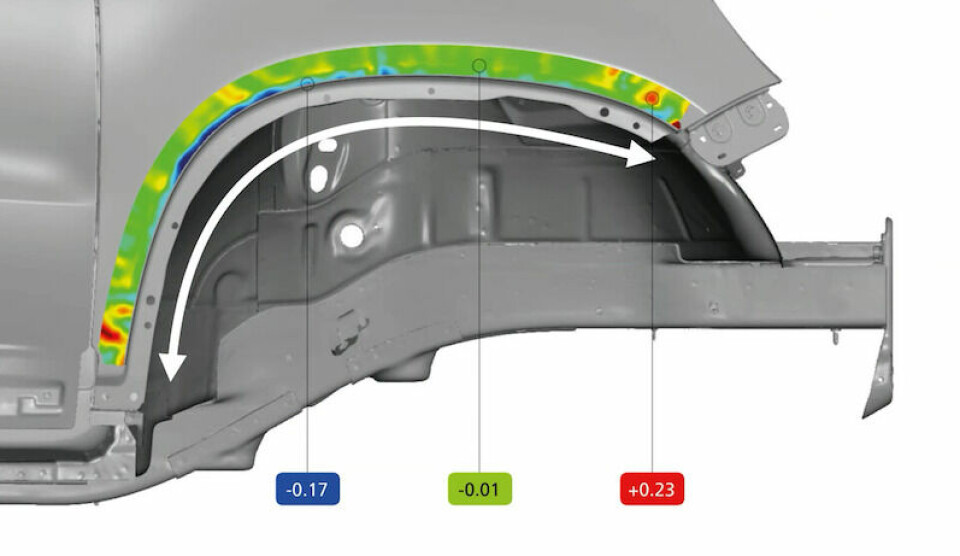
ATOS 5X for Automotive Car Body InspectionThe systems reach their maximum efficiency in automated applications such as the ATOS ScanBox series. For example, an ATOS 5X in the ATOS ScanBox Series 8 accelerates a process by a factor of four when measuring and inspecting large and complex objects. The automated measurement of a complete car body both outside and inside typically takes 30 minutes with ATOS 5X – including the precise coverage of complex geometries. The system enables the highest possible throughput, with the main application areas in Meisterbock and Cubing, inspection of complete vehicles and quality control in body manufacturing. ATOS 5X delivers full-field data for comprehensive process and quality control of hang-on parts, side panels and complete car bodies.
With full-field 3D data you can:• Visualise how components from different suppliers will fit together through Digital Assembly• Control series production with Trend Analysis using Golden Master models• Inspect and classify surface defects on sheet metal components and tools• Reduce fixturing costs with Virtual Clamping•Visualise complex evaluations using Augmented Reality
Find out more at www.gom.com/inspect
Full-field 3D measuring data as a condition to realise ‘smart’ factoryThe measured results increase process reliability and serve as a control element in the process chain. The actual state of the measured parts is completely digitised so that all process parameters can be specifically checked and adjusted. Full-field digitalisation thus forms the basis for intelligent manufacturing. Within the modular structured smart factories of Industry 4.0, cyber-physical systems monitor physical processes, create a virtual copy of the physical world and make decentralised decisions.This makes clear what measuring technology has already done so far and will do in the future. It is no longer just a question of improving product quality, but of improving the entire production process. It is obvious that standardisation and transparency in global product development processes will play an even more important role. The aim is to ensure that all information that affects the vehicle manufacturing is always digital existent and ready-to-call at all times, from the design phase to the finished car. Only this can guarantee that in future, a manufacturing order could be automatically controlled in line with the digital value chain. No more drawings will be needed since each produced component will be measured completely in 3D. Thus, component faults will automatically be measured and corrected during the car manufacturing process.