Interview: John Pacanovsky, Scigrip
As the use of composites increases in the automotive industry, the head of R&D at an adhesives supplier talks about the advantages of this type of bonding
AMS: Scigrip does some work with Renault and Fiat trucks, is that correct?
John Pacanovsky (JP): Whilst we can’t name specific models, Scigrip is a supplier of smart adhesives to some of the top European OEMs as well as a number of tier ones which also supply into the many truck and bus manufacturers. In each of these applications, our key products are used to bond carbon fibre composites to metals. We also sell our special adhesives to high-performance automotive manufacturers in Europe.
AMS: Can you talk a bit more about what you do with Renault and Fiat?
JP: No, but we do most of the heavy truck business and we have the bus industry and the rail industry, and a lot of that is metal-to-metal bonding.
AMS: Does Scigrip supply the kind of adhesives that can be used for the bonding of carbon fibre parts, such BMW is doing for i3 production?
JP: Yes, we do supply adhesives that would work in those cases. The biggest challenge for bonding, especially bonding metal to carbon fibre composites, is that they have very different strengths and very different thermal expansion coefficients (CTEs); when they heat up and cool down they expand [and contract] at different rates.
First of all, when using mechanical fasteners you get point loads along the bottom line, so it would be a point and then no bonding, another point then no bonding, then another point; whereas adhesives will distribute the load across the entire bond. So that’s one of the reasons why adhesives are beneficial.
"Bonding composites to a metal structure is where MMAs really shine"
– John Pacanovsky, Scigrip
In addition, it’s quite difficult to mechanically fasten a composite structure. If you drill a hole for a bolt it will vibrate over time and it will loosen, and so with composites, structural adhesives are always beneficial because they allow you to keep the structural integrity of the composite part.
AMS: And presumably there are weight-savings if you don’t have to use bolts?
JP: There are weight-savings, although this is less important than the elimination of stress concentrations. In a point loaded mechanical fixture there is also the ability for moisture or air to get into the joint unless the fixture comes with a sealant or gasket, whereas an adhesive will seal the bond line against fluids – doing two jobs with the same product. And that helps with corrosion resistance, especially metal-to-metal type bonding.
AMS: What kind of curing times are involved?
JP: So the three main types of structural adhesives used in automotive are: epoxy, polyurethane and structural methacrylate, which is what Scigrip offers. Both epoxy and polyurethane have a wide range of cure times but in almost all applications they either need to be heat-cured or to have a heated post-cure to achieve their full properties. The structural methacrylates actually allow for room temperature curing, so we can offer a room temperature cure, a structural bond, in five minutes all the way up to 90 minutes. And there’s never a need to have post-baking or heat curing with structural methacrylate.
AMS: So these are MMAs [methyl methacrylate adhesives]? Are these a new development?
JP: The technology for MMA was developed back in the ‘90s but the technology has really advanced within the last few years.
AMS: What changes have occurred?
JP: Developments include a much higher toughness of the adhesive bond. Engineers will look at a stress-strain curve to see how much stress a bond can absorb before it strains and fails. There’s a distinct difference between the way even toughened epoxies and urethanes look, and how the MMAs look. They [MMAs] can absorb far more energy and are far tougher than both those types of structural adhesives.
An epoxy adhesive will have, traditionally, 3-10% elongation at its highest point (the shear failure) but structural methacrylates can have over 100% elongation whilst still maintaining a high structural strength, so this allows for far more energy absorption and makes a far tougher bond.
Another strong improvement is the range of lower surface energy materials that can be bonded with MMAs. This not only makes surface preparation easier, avoiding the need for priming steps, but also permits designers to look at a wider variety of plastics to consider for assembly by bonding.
AMS: So Scigrip’s work involves developing the chemical composition of these adhesives?
JP: Yes. We look at the applications, what we actually need to bond: what the substrate is – whether it’s metal to metal, whether it’s metal to a composite, whether it’s composite to composite; and then the surface temperature, the surface requirements. Most marine, automotive and wind energy applications have to have a very high toughness, and so that’s how we design our structural adhesives.
AMS: And do you look at the equipment needed to apply the adhesives?
JP: Most high-volume adhesive applications are dispensed from a large pump system. We can supply them out of cartridges, which would be with an applicator gun, but most high-volume applications are with a pumping system. Very large automotive applications would be robotically applied.
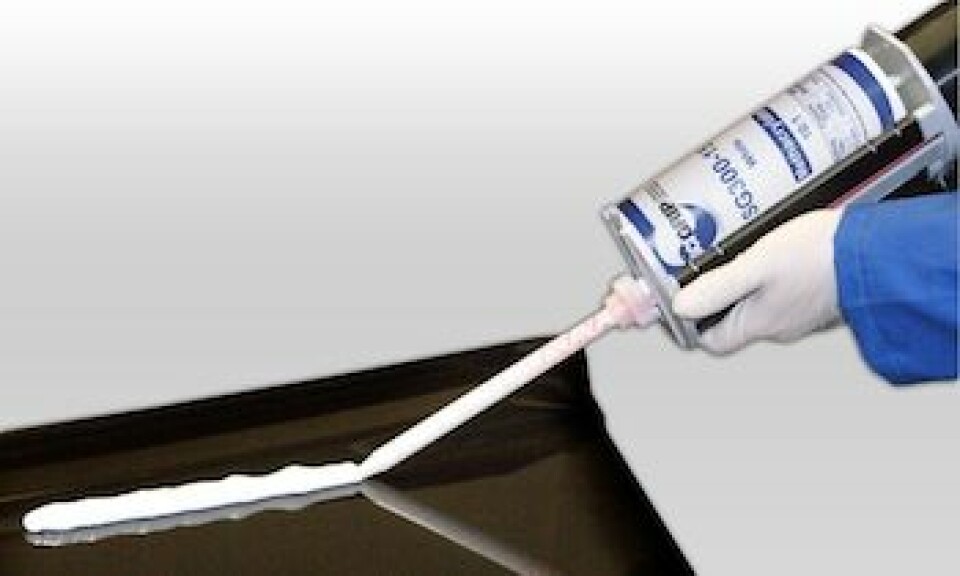
AMS: So the growing trend for automotive manufacturers to use composites must be good news for Scigrip?
JP: Yes, especially when we are looking at having to bond composites to a metal structure – that’s where MMAs really shine. It’s too early to tell where the composites market is going, but we are poised to take advantage of the growth in the composites sector of transportation as well as other industries where resistance to fatigue is a challenge.
AMS: Do MMAs offer any additional benefits?
JP: In the weight reduction area, going to composites is a benefit versus metals to begin with, but then as the composite – or regular plastic materials – get thinner to continue to take weight off, going to a lower exotherm, a lower shrinkage product, is beneficial because of bond-line read-through.
On the opposite side of where a thin panel is glued you can normally see deformation of the part due to shrinkage of the adhesive, or due to the heating of the part, so going to a lower bond-line read-through is going to be beneficial as the parts gets thinner; it makes for more aesthetically pleasing parts. In some cases, the panel thickness is limited by the need to avoid this distortion, so low read-through bonding saves on total panel cost while improving aesthetics.