Interview: Atterby and Burton at Luxus
Peter Atterby, managing director, and Terry Burton, technical manager, discuss Luxus' commercialisation of a new range of lightweight polypropylene polymers for interior trim, featuring up to 60% recycled content
Joanne Perry (JP): Luxus has been supplying thermoplastic materials to the automotive industry for 30 years. Which of today’s models feature Luxus products?
Terry Burton (TB): So, for Nissan we have the Note, Qashqai, Juke and Leaf; Honda, the Civic; JLR, the Evoque, the Freelander, Range Rover and Jaguar EF; BMW, the Mini convertible; and Toyota, the Avensis.
JP: Which interior components are you referring to?
TB: It can be the centre console, door panel, steering wheel cowl, A and B posts – which are all A-surface finish, so they have to have a scratch-resistant, perfect finish, with no white or black specking and no interruptions to the texture.
JP: You have reduced the filler content in your compounds as a lightweighting strategy. Can you explain exactly what this means?
TB: So, we take the filler content that could be maybe 20 or 25% mineral, reduce that filler content but then maintain the mechanical properties of the polymer, particularly on the tensile and flexural modulus. So the part is as stiff without the filler as it was with the filler, which is important especially for the door panel and the centre console. Reducing the filler reduces the weight of the part.
Peter Atterby (PA): The problem with the mineral filler is that it is very heavy. When we are trying to lightweight [the product] we take out the heavy components, but the mineral filler is in there to maintain dimensional stability at higher temperatures in the application, so when you use it above the waistline [of the car] it can’t distort at less than 110°C and below the waistline at less than 80°C. So we are taking the heavy component out of the mix, then trying to replace that with something that would give the same dimensional properties but at a much lighter weight.
JP: When was the Hycolene range first developed, and was this originally for the automotive industry?
TB: Yes, we developed that specifically with automotive in mind because of the need from legislation to reduce CO2 emissions. We knew it would fit that market sector, so we developed the product based on highly filled grades, [then] reduced those fillers, maintaining the chemical properties and lightweighting it. We began [development] in 2011.
PA: Hycolene isn’t just one product, it’s a range of grades within an overarching trademark. Whilst we started in automotive, we hope we are going be able to extend it into some consumer goods as well.
JP: So the development process started off in-house but you now have a number of collaborators: Coperion, IAC and then JLR for the final testing. Can you give details of Coperion’s role?
TB: Obviously, the supply of the [new] machine [a twin-screw, co-rotating extruder]. They will also help us with the technology for mixing materials, because this is a brand new way of formulating and we need to integrate these fillers – these reinforcing agents – into the polymer.
PA: It’s not just the extruder, we’ve bought the feed system from K-Tron, which is now a Coperion company, so what we are trying to do is to pull together the skills of them both to solve some particularly difficult problems. So they’ve done things like screw configurations for us and they are contracted to do even more work to improve the product once it's got to the next stage of beta testing.
What we get from them is the input on screw designs, dispersion of product and how we might do it; we know what we want to achieve but they have more experience in terms of process control. When you buy an extruder like that, everything’s interchangeable, so the screw configuration can be changed because all the segments are completely different. So we will take bits off and put bits on to create a different process and technique whenever we want to.
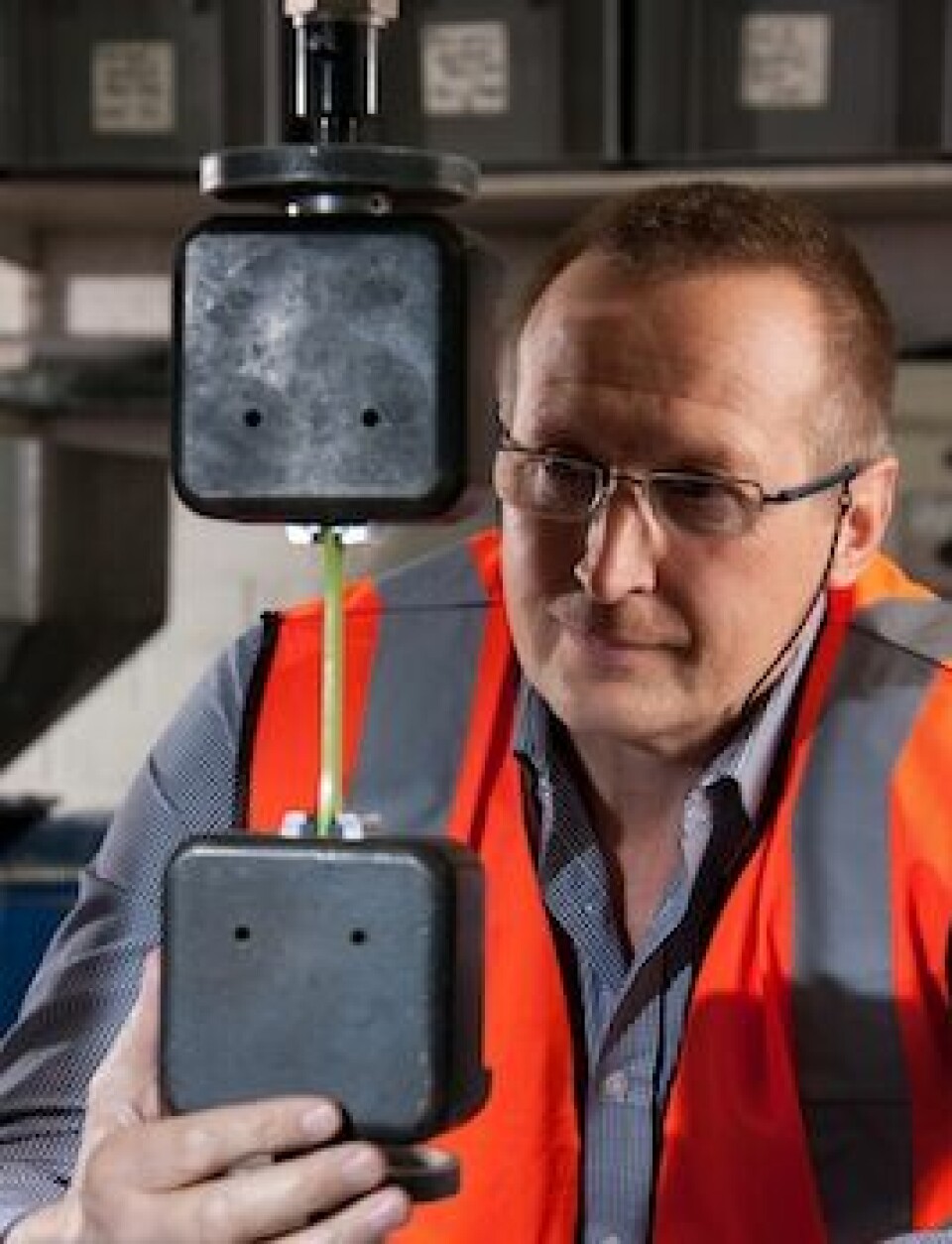
JP: What is the contribution of IAC?
PA: IAC are the moulder to JLR, and IAC are our partners for the initial testing of the material onto actual components within the car, and it will develop from there.
JP: Why was JLR the OEM which became a partner for the commercialisation process? [Early trials with existing client Renault-Nissan focused on the formulation of suitable grades.]
PA: The way we see this product going globally is the big issue for us. JLR’s research and development is based here in the UK. We felt that JLR were the right partners for us on this particular project, because it is a luxury brand with an interest in the next generation of lighter, stiffer, scratch-resistant products and they are looking at their environmental credentials going forward.
TB: JLR don't have interior grades at the moment, so it's a whole new project for them; our other automotive clients have quite a lot of interior grades currently. If we can get into JLR, it’s a whole new market.
JP: Which JLR models might be used in trials?
PA: We don’t know at the moment. The components that we will put on test will be from existing models, and in fact they might actually be models that are no longer in production, but there’s a debate going on at the moment. I think it’s going to be current production models.
TB: JLR have put some proposals forward to IAC and IAC are just deciding, because it’s all about moulding time as well.
PA: The difficulty that we have is that IAC are up to capacity because of the demand from JLR, so we have to try and find components that we can get test time on, basically. So we don’t yet know whether it will be on a current model – that is the favoured option – or whether it will be on repair parts for older models.
JP: What are the main stages of the Hycolene manufacturing process?
TB: Hycolene has to be processed in a certain way. So, we have to have the polymer melt at the correct point and then – we don’t want to give too much away, but we have to introduce the additives at the right point in the melt flow to create the right stiffness of the product, so we actually get the right tensile and mechanical properties.
That is the critical bit and why we are also working with Coperion, because we’ve done this on a lab scale; now we have to produce this on the new machine. Our lab machine is 50kg an hour; the new machine is going to be two tonnes an hour, so that scale and getting the products in at the right point in the process are absolutely critical.
JP: Peter, you have previously referred to a “fundamental step-change” in technology as filled compounds are replaced by reinforcing additives. Can you explain more fully?
PA: The main thing is the way the market’s changing. So the step-change is in the feedstocks that are available to us and our projected feedstocks for the next ten years, because there’s been a complete change in the way that the market has reacted to waste being generated in society.
Moving forward to the technologies that we will be using on this machine, we start with the feed systems – and the feed systems are completely different to what we would have done in the past on this type of machine. The big step-change for us is across the board in terms of the machine technology, the machine design, the polymers that we will be processing, the way we will be feeding and the way we will be formulating them together.
JP: How soon do you expect to reach the planned capacity of 12,000 tonnes per year?
PA: The big problem is the fact that this is a commercialisation project; 2017-18 is when we think that will happen but it does very much depend on the success of the next stage of the process and the willingness of the automotive companies to buy the product, at the end of the day.
JP: What proportion of the plant’s total output of 45,000 tonnes currently goes to the automotive industry?
PA: 30%.
JP: Is that into the UK automotive industry or further afield?
PA: The European automotive industry. We are developing a model for licensing and globalisation of the product as part of this project which may see us create joint ventures in other countries.
JP: Output is currently limited by local sources of recyclate PP; do you see that situation changing?
PA: If we are going into a new market, we think [it] will start with us shipping the whole product, but then we will encourage and create situations where we improve the recycling capabilities in those areas, because in some economies it isn’t developed.
JP: Is there any possibility of pushing the recycled content beyond 60% in future?
TB: Yes, absolutely. The critical factor is that we are making a compound that is fit for purpose. We can make materials now that are beyond 60% but it is always down to the specification.
PA: We use the non-recycled content to adjust the technical aspects of the product, so 60% is a fairly high level for this type of component but there might be other markets in which it would be easier for us to push that level up. And of course there will be different levels in different grades types as we develop the Hycolene range.
The vehicle lightweighting trend, which is being fuelled by stricter environmental and efficiency requirements, has seen carmakers developing materials such as aluminium and carbon fibre as alternatives to steel. But suppliers, too, are searching for innovative solutions.
At its technical compounding and recycling complex in Louth, Lincolnshire, Luxus is in the process of commercialising a range of lightweight polypropylene (PP) compounds for the interior trim market, with the help of a £600,000 ($905,000) grant from the EU. Made from as much as 60% recycled content, these Hycolene additives are claimed to offer a weight saving of up to 12%, improved scratch resistance and tensile properties which safeguard the appearance of the moulded compound.
The EU 50% fund has assisted the commercialisation process and the purchase of a new, twin-screw co-rotating extruder from Coperion which can produce two tonnes of product per hour, potentially enabling Hycolene output to reach 12,000 tonnes a year. The new machine sits in the company’s 2,681 sq.m Compounding Centre, along with a twin-screw machine from Bestorff and one from Maris, plus three single-screw extruders supplied by PRT and Falzoni.
Luxus receives recyclate feedstock from across Europe, and after sorting and cutting this is progressively reduced in size by shredding machines installed at the on-site 1,466 sq.m Recycling Centre. A Vecoplan shredder operates at 1,500kg per hour, while two Zerma machines process material at 1,000kg and 2,000kg per hour. There is also a film processing line based on shredding and single-screw extrusion which uses equipment from Erema, running at 1,500kg per hour.However, it is the Compounding Centre which houses the crucial blending and extrusion operations. Together with virgin feedstock, the shredded, recycled material is heated at temperatures of 200-270˚C inside the extruders, which also filter out contaminants using wire mesh. The exact mix of virgin and recycled content, which varies according to the source, is decided in the Technical Centre, a 451 sq.m laboratory containing: an FTIR (Fourier transform infrared spectroscopy) material identification system; twin-screw prototyping compounders; a computerised colour-matching injection moulding system; and testing equipment.
The end result is small pellets of plastic which are bagged up and delivered to injection moulding companies for the manufacture of interior trim components.
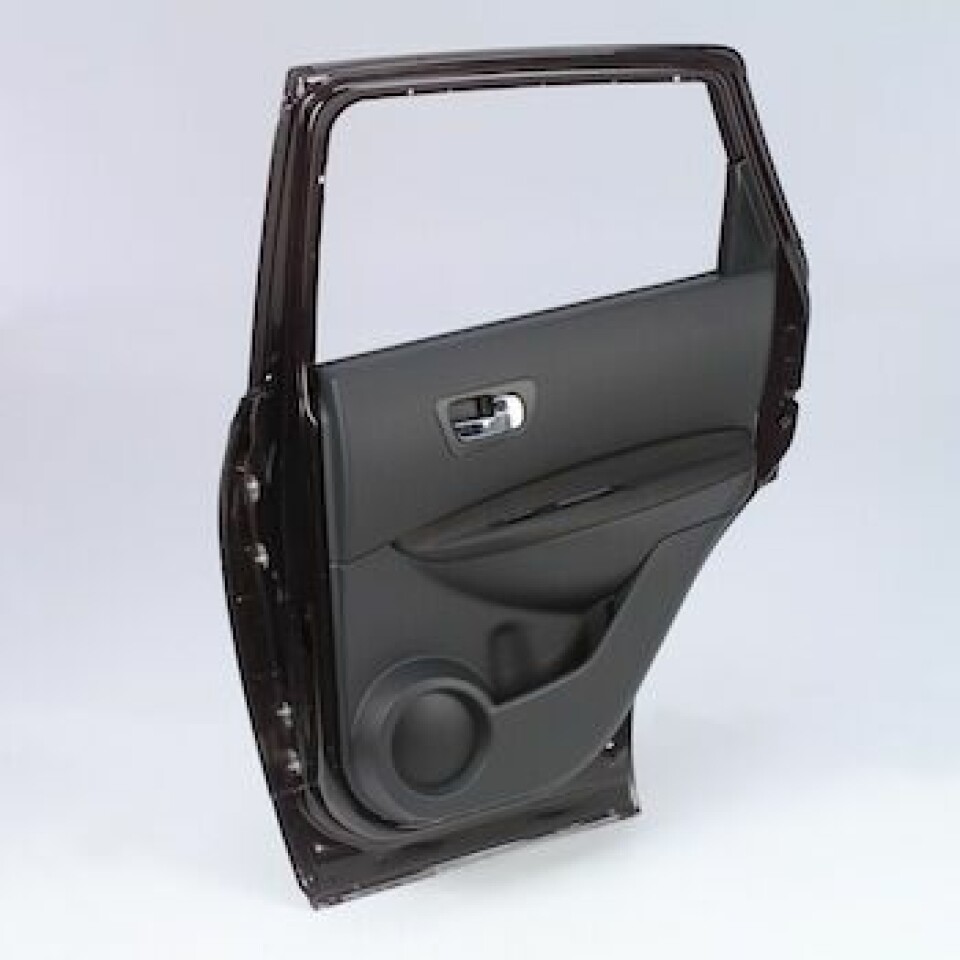
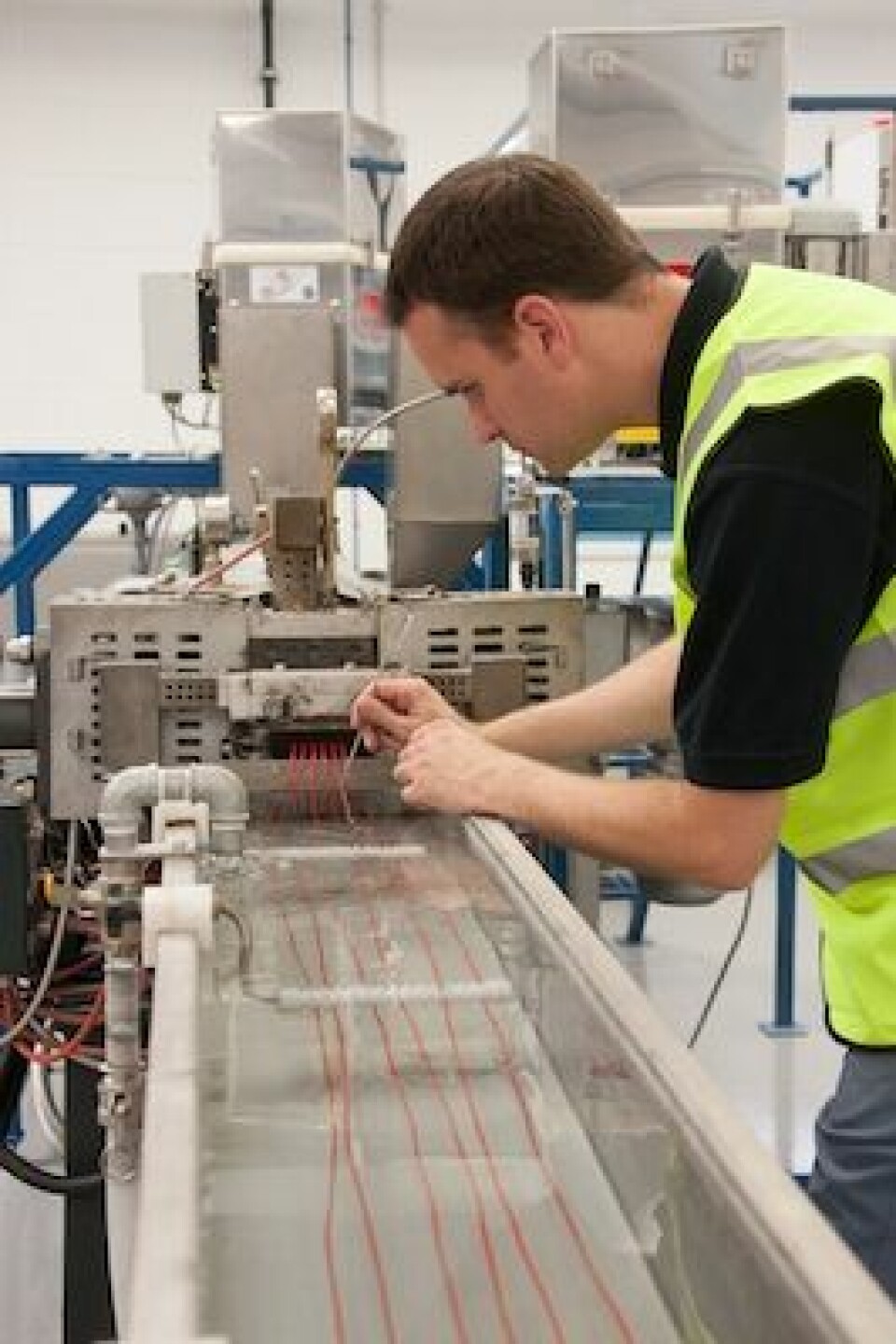