Hitting the gas

As OEMs step up their sustainability programmes, two leading players are arriving at key milestones. AMS reports on how biogas projects have contributed greatly to the renewable energy success of GM and BMWLast year, for the first time, the BMW Group met the majority of its electrical energy needs by using renewable sources – a significant step on the way to reaching its target of 100% green power. The vehicle-maker appears to be making rapid progress; by March this year, just 12 months later, the proportion of electrical power it took from renewable sources had risen from 51% to 58%.
“We have a clear objective and a concrete plan for the transition to renewable energy,” said Ursula Mathar, BMW Group’s head of Sustainability and Environmental Protection, on the release of its Sustainable Value Report last year. She warned, however, that “economic viability” and establishing “the right framework conditions” will be essential for the continuation of BMW’s step-by-step plan: to improve energy efficiency at its facilities worldwide; to install sources of renewable power; and to purchase green energy from third parties.
In 2015, BMW for the first time took over half its electrical power from renewable sources. By March 2016, the proportion had reached 58%
In its latest Sustainable Value Report, released in March this year, BMW claimed a reduction of 36% in energy use at its plants since 2006, with consumption per vehicle produced dropping by 2.7% to 2.19MWh in 2015 compared with the year before. Renewable power installations now include solar arrays, such as at Mini Oxford in the UK, wind turbines at Leipzig in Germany, hydropower at the joint venture SGL Automotive Carbon Fibers in Washington and biogas projects at both Spartanburg in South Carolina and Rosslyn in South Africa.
BMW stated in the report that its strategy is not to focus on any particular renewable source but to harness different technologies: “We decide at each location which concept makes the most sense in view of local conditions”. However, the OEM specified that one plan is to install photovoltaic systems at its German plants over the coming years.
GM shoots for the starsAlso in March, another leader in renewable energy, General Motors (GM), won a fifth Energy Star award from the US Environmental Protection Agency (EPA) for improving its energy efficiency. In 2015, the vehicle-maker reduced energy consumption per vehicle at its US factories by 5.6% to 1.9MWh. “We’re continually in pursuit of innovative technologies to reduce the environmental impact of driving, as well as practices that lessen the carbon footprint of manufacturing those vehicles,” commented Jim DeLuca, GM’s executive vice-president of Global Manufacturing.
When making its first serious commitments to renewable energy in 2011, GM set a goal of reaching 125MW of green power per year by 2020. Between 2013 and 2015 the OEM invested around $36m in onsite projects, and its portfolio now includes: solar arrays at 22 facilities, generating 48MW of power; solar charging canopies for electric vehicles (EVs) at nine locations; three landfill-gas installations; and one waste-to-energy project.
In 2016, GM will surpass its target of reaching 125MW of renewable energy – four years early
Upcoming wind programmes in Mexico and the US will provide GM with a further 34MW and 30MW per year respectively; at Arlington Assembly, Texas, this will mean the production of 125,000 SUVs per year using wind power. The OEM is also moving into the ownership of solar arrays rather than relying on purchase agreements and recently commissioned a 1MW project at Bowling Green, Kentucky. One mainstay of its renewable energy strategy from the very beginning, and still a strong contributor today, is biogas. Thanks to projects in Ohio, Indiana and Michigan, the vehicle-maker is now one of the largest industrial users of landfill gas in the US.
GM now benefits from at least 105MW of green power supplying its facilities, and by March this year its decades-long exploration of renewable energy had not only helped to reduce its environmental footprint but to generate savings of $80m. According to Rob Threlkeld, GM’s global renewable energy manager, the two wind projects coming online later this year will take the OEM beyond its 125MW target.
One renewable energy project highlighted in BMW’s Sustainable Value Report from March 2016 is located in South Africa, at the Rosslyn plant in Pretoria. This factory, which is switching from 3 Series to X3 production with a 6 billion rand ($408.3m) investment, received its first green power in October 2015 after the signing of a ten-year purchasing agreement with Bio2Watt. This start-up energy company operates a biogas plant on agricultural land in Bronkhorstspruit, 50km east of the capital, where it receives waste from cattle and chicken farms plus the nearby city of Tshwane, as well as benefitting from storm water collection dams.
The organic waste is fed into two anaerobic digesters to produce biogas, which then goes to a gas engine to generate electricity. This is directed into the power grid for uptake by purchasers such as BMW. Currently, 40,000 tons of cattle manure and 20,000 tons of mixed waste are being converted to biogas feedstock for a combined heat and power application. The Bio2Watt plant has the capacity to generate 4.4MW, and BMW Rosslyn will now take 25-30% of its energy needs from this renewable source. In the last few months of 2015, 3.1GWh were supplied, representing 4.5% of the electricity required by Rosslyn.
Speaking at an event to mark BMW Rosslyn’s first use of green power, Sean Thomas, CEO of Bio2Watt, commented: “Because this had never been done before in South Africa, it has been an extraordinary eight-year journey to reach this point.” He added: “Biogas is a storable form of renewable energy, capable of being transported and utilised 24 hours a day, seven days a week. For this reason, biogas is capable of providing energy on a small scale but can be expanded to large-scale, centralised production.”
Long before BMW started using biogas at Rosslyn in South Africa, it was already operating a significant programme in the US at its Spartanburg production hub for SUVs. This plant is already the largest by volume in BMW’s global network and turned out a record 400,904 units last year, a 15% increase on 2014, but it is set to grow still further. A $1 billion expansion programme at the 6m sq.ft facility will see the existing X models joined by the new X7 and a capacity increase to 450,000 units per year. It is therefore quite an achievement that arguably the OEM’s most important factory, responsible for producing about one in five BMW vehicles, now meets half its energy needs by using landfill methane.
The gas-to-energy project, developed by BMW together with its partners Ameresco and Waste Management, came on stream in 2003 and has saved BMW an average of $5m year in energy costs. The alternative energy system captures methane from the nearby Palmetto landfill and uses it to efficiently cogenerate electrical power and heat water; the pressurised gas is transported by pipeline to the Energy Center at Spartanburg.
The gas was used to power four turbines at the Energy Center until 2009, when these were replaced with two more efficient versions which boosted electrical output from 14% to almost 30%. This upgrade eliminates CO2 emissions by 92,000 tons per year and provides additional cost savings of $2m.
In addition, since 2013, Spartanburg has met all its material handling needs in production and logistics by using a 350-strong fleet of hydrogen fuel-cell forklifts, having installed a storage and distribution area near the Energy Center in 2010. This saves the plant 4.1m KWh of energy per year.
Landfill gas was the focus of General Motors’ (GM) very first renewable energy project in 1993, at the 2m sq.ft Toledo Transmission plant, Ohio. The OEM subsequently investigated its use at other sites close to landfills and established similar projects at its vehicle factories at Orion, Michigan, and Fort Wayne, Indiana.
The 4.3m sq.ft Orion plant, which makes the Chevrolet Sonic and Buick Verano, has been using landfill gas since 1999, meeting almost half its energy needs for production since 2011. Fort Wayne, covering 3m sq.ft and turning out GMC Sierras and Chevrolet Silverados, began a landfill gas programme in 2002 and in 2011 commissioned another boiler to boost the proportion of landfill gas used from 15% to 21%.
In 2014, the Fort Wayne and Orion programmes progressed further through GM’s investment in equipment to generate electricity onsite; gas that would have been flared at the landfill is now redirected to the plant, a more economical solution. The two projects together provide 14MW and cut C02 emissions by 23,000 tons each year. As of March 2016, they are also saving GM $6m per annum.
Indeed, GM’s recent appointment by the EPA as a Green Power Partner for its efforts to advance clean energy was due in no small part to the Fort Wayne plant, which has been ranked by the agency as a top-30 generator of onsite green power. Fort Wayne now meets one-third of its energy needs through methane; at Orion the proportion is closer to two-thirds; at Toledo the figure is about one fifth.
At 4.1m sq.ft, Detroit-Hamtramck in Michigan is one of GM’s largest North American facilities. It is now also one of its key renewable energy performers, having benefitted from an arrangement with a third-party waste-to-energy (WTE) plant since July 2014, when it became the first GM factory to power its operations from such a source.
Currently the maker Chevrolet and Cadillac models, Detroit-Hamtramck was previously the only GM site in North America which burned coal; in 2013 the plant replaced its two antiquated boilers with an 8,000ft pipeline carrying steam from the Detroit Renewable Power (DRP), in collaboration with DRP and the Detroit Thermal utility company, plus their parent company, Detroit Renewable Energy.
The WTE facility receives 900,000 tons of municipal solid waste per year as well as non-recyclable by-products from GM itself. These are converted into refuse-derived fuel to power DRP’s boilers and produce 5.3m pounds of steam per year, 10% of which is allocated to Detroit-Hamtramck. After coming online in July 2014, the system started generating 16MW of renewable energy, which the plant now uses for heating and cooling systems as well as process operations. The steam supplies three 4,000-ton, turbine-driven chillers, a heat exchanger, an air compressor and a humidification system in the paintshop.
The 15-year contract with DRE enabled GM to avoid $6m in capital investment as well as ongoing costs associated with steam production. On implementing the pipeline, OEM estimated that CO2 emissions would drop from around 76,000 to 19,000 tons per year; moreover, Detroit-Hamtramck no longer needs to send coal ash to landfill. Together with small-scale solar installations, the plant now meets over half its power requirements from renewable energy.
According to Rob Threlkeld, GM’s global renewable energy manager, the implementation of the projects at Detroit-Hamtramck, Fort Wayne and Orion put the OEM on track to produce 125MW of renewable power per year by 2020. Speaking at the launch of the Detroit-Hamtramck pipeline, he acknowledged GM’s changing mix of energy strategies but added: “Landfill gas and waste-to-energy will still be the largest components of that 125MW goal.”
Dag Hoeft, process industry technical sales consultant, Mitsubishi Electric Europe, explains how virtual power plants can ensure that supply matches up to generation when it comes to renewable energy
AMS: In simple terms, what does a ‘virtual power plant’ consist of?DH: A virtual, or hybrid, power plant is when a group of power plants are controlled as one, using the same software platform. It typically combines multiple energy sources including renewables, and in the near future, energy storage facilities. Each individual power plant may have a variable output due to tides or weather conditions, for example, but the virtual power plant solution will control and coordinate these plants to deliver constant and reliable power to the grid.
AMS: Why would a virtual power plant be necessary; what would it achieve?DH: Variable and renewable power sources are becoming more and more common in the energy market. Their lack of consistency (the sun and wind are not under our control) has to be managed to create a stable and reliable grid/power supply to the energy market. That is what a virtual power plant application is doing.
For large manufacturing sites with their own power plants, such as automotive production sites, renewable sources can be balanced with other sources that are geographically separated and produce a stable but varied power supply. Additionally, it makes the overall purchase price lower when consuming energy, as any excess can be sold back to the grid more effectively.
AMS: Could a virtual power plant be used to control power from biogas?DH: Yes! Biogas is a popular renewable source and can be an essential component of virtual power plant set-up. Our demo shows how biogas performs an important role in a virtual power plant application. The power supply from the photovoltaic plant and wind turbine depends on weather and daylight, making it volatile. The power supply from the biogas plant is controllable. A virtual power plant application can be used to control the power supply from the biogas plant and ensure that the total power supply from the photovoltaic plant, the wind turbine and the biogas plant meets the demand of the grid seamlessly.
AMS: Are virtual power plants just a theory? Or, how soon would Mitsubishi envisage implementation?DH: Virtual power plants are not a theory – they are live! Scrolling though the net, you’ll find a lot of running virtual/hybrid power plant examples. For a high profile real-life example, Mitsubishi Electric has installed a virtual power plant application running at one of the largest airports in Germany, providing and controlling power to the airport.
The advantage for customers using the solution from Mitsubishi Electric is that the virtual power plant application is supported by a full range of automation hardware and software that can be implemented in order to improve control, monitoring and interaction with a number of energy sources. This includes a range of PLCs [programmable logic controllers] that starts with small, distributed units and stretches up to powerful units that can manage tens of thousands of inputs in near real-time and are used for controlling conventional power plants. There is also a wide range of inverters, HMIs [human-machine interfaces] and other software products that can be integrated to provide energy saving and maximise on efficiency.
AMS: Has Mitsubishi collaborated with vehicle-makers to explore the use of virtual power plants in the automotive industry?DH: Actually not with vehicle manufactures yet, but car plants are on the agenda and not so different from big projects such as airports, which are already live. Vehicle manufacturers could easily benefit from a virtual power plant application. Some of them own their own fossil fuel power plants to feed their production needs and are actively investing in biomass, wind and solar technologies.
Combining and controlling these power sources with a virtual power plant application would certainly decrease overall energy costs and reduce the carbon footprint of the enterprise as whole. Both of these benefits would also provide positive messages of efficiency and sustainability, which are part of the philosophy of most mainstream manufacturers.
Electric vehicles are also going to be a much bigger part of our future and producing green energy for the cars they make can only be one step away.
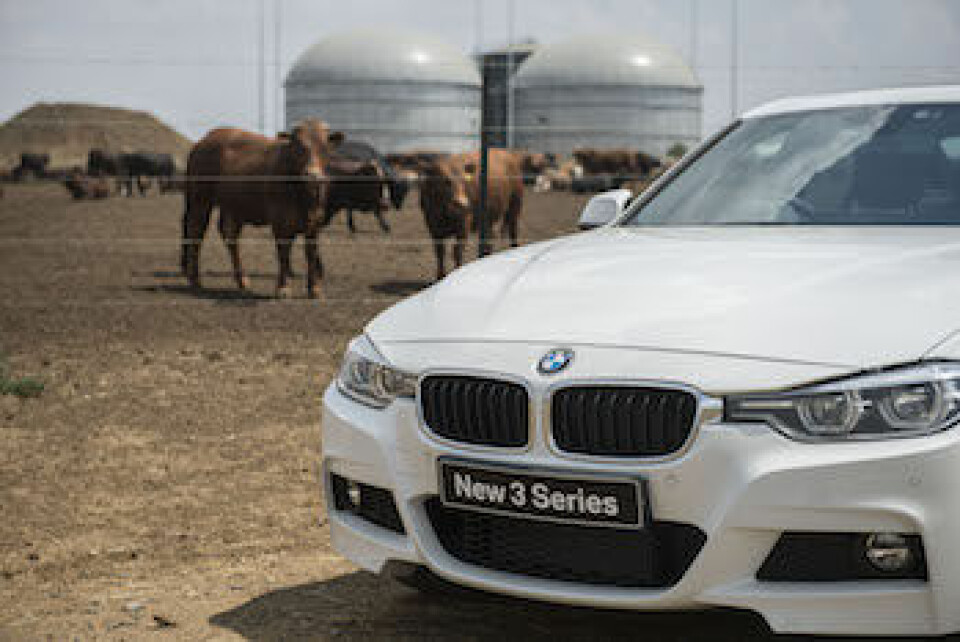
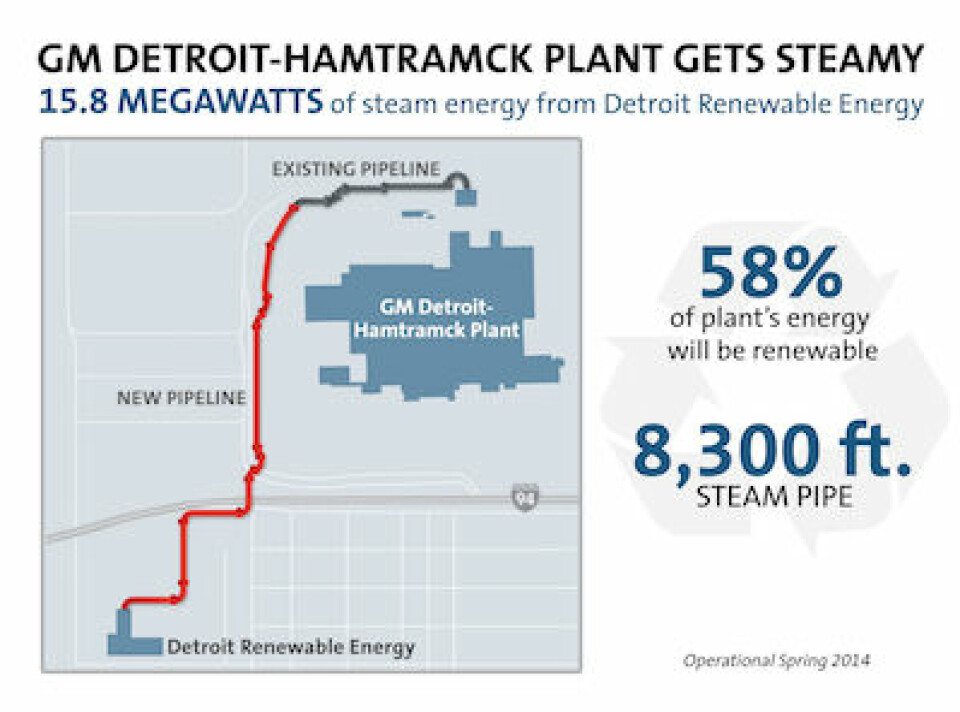
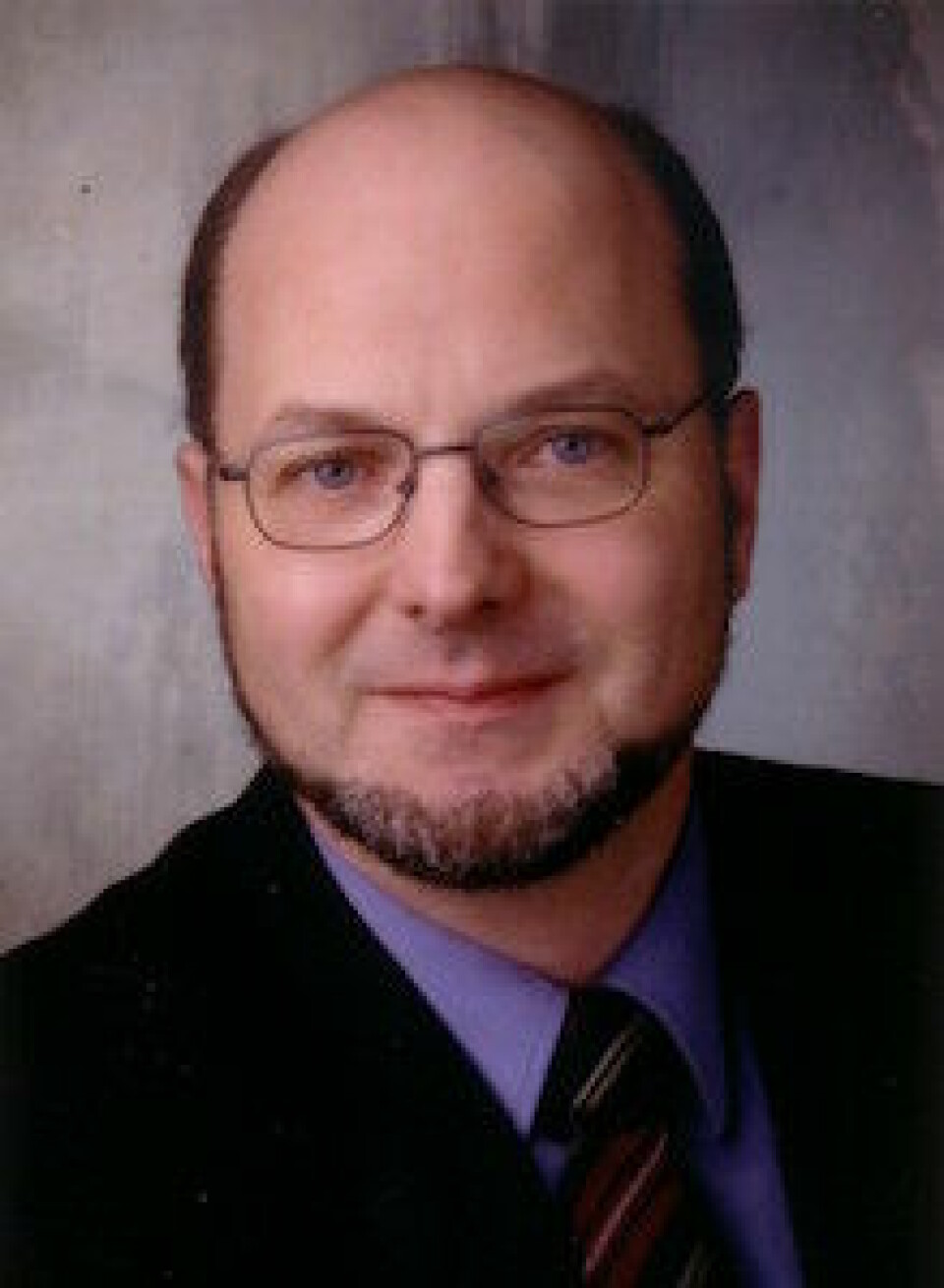
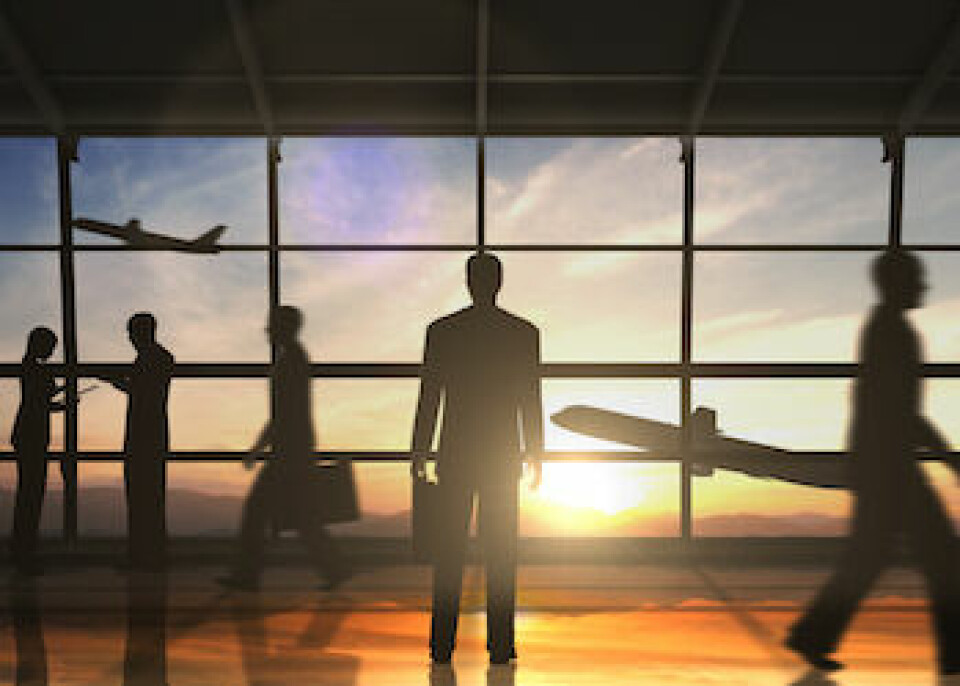