Fit for automated purpose
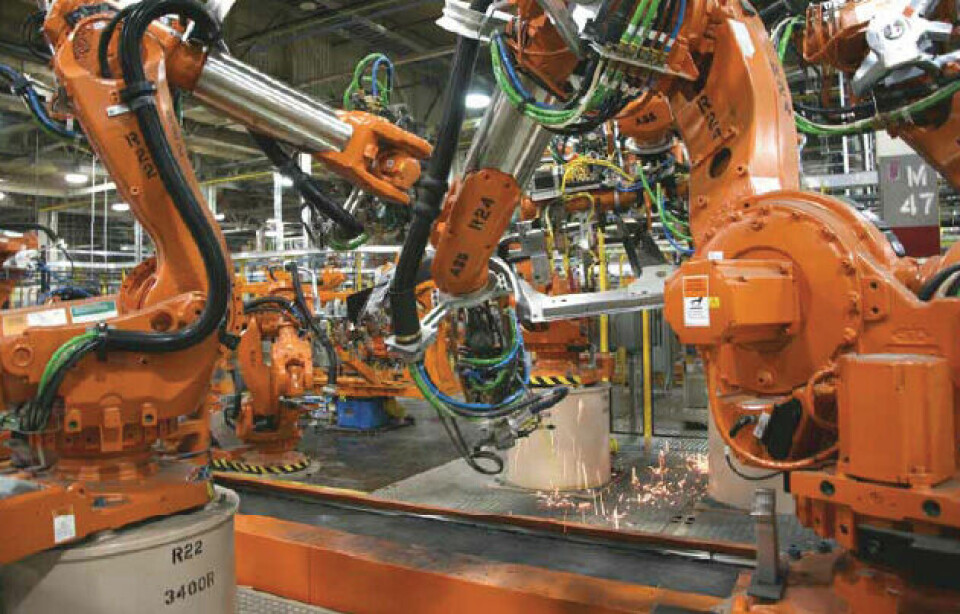
There was a time when ‘hard’ automation – tailor-made, dedicated installations – was the trend, but things are moving to a more flexible approach
It appears that the use of robots in the automotive manufacturing sector is entering an unpredictable period of fluctuation. Figures released last year by the International Federation of Robotics (IFR) indicated that from 2005 to 2006, purchases of robots by the worldwide automotive industry fell from just over 24,000 units to 20,000.
The reduction was particularly evident in the US, but there were also sales declines in Europe and Japan. The Chinese and Korean automotive sectors maintained and even increased their level of robot acquisition over the past 12 months. Two thousand and five was a boom year for the robotics industry in general, which was bound to be followed, sooner or later – sooner, as it happened – by a comparative downturn. Yet there are already indications that the apparent slump could be reversing or, more precisely, reconfiguring itself.
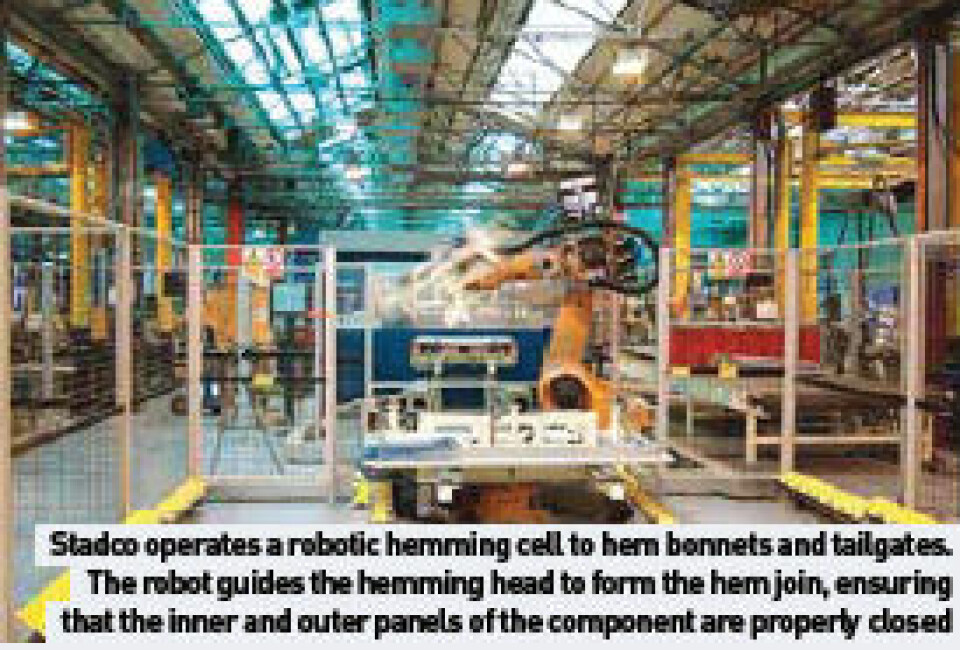
In June, the Germany-based IFR released preliminary information about 2007 sales of robots to the automotive sector. The US market showed an increase in purchasing against a background of static worldwide demand. Robot purchases by the automotive industry across the US, Canada and Mexico jumped by an astonishing 52 per cent from 2006 to 2007, representing a total of 6,200 units. The IFR also noted what it described as “heavy investment” in robots by the German and Italian automotive industries, although details were not given. Paul Meeson, Manufacturing Engineering Director for UK-based Stadco, a Tier One pressings and component supplier, puts forward key words such as ‘flexibility’ and ‘reusability’. He says there is a perceptible move away from the use of ‘hard’ automation – tailor-made dedicated installations for carrying out fixed sets of procedures. Flexible and reprogrammable robotic cells are at the forefront now.
Greater product variety
The main advantage of this approach is that the same set of hardware can be used to carry out different, if related, sets of procedures on different assemblies, so that a single line can handle greater product variety. Initial capital expenditure will probably be less that for inflexible equivalents and in extreme cases, the individual robots could be set up for completely different tasks. Meeson pinpoints a specific application in which robotic technology is now removing the use of hard automation – that of hemming, where an outer panel is folded over an inner one. This used to be an operation requiring dedicated presses or even manual tabletop units, but Stadco has been operating a robotic hemming cell for an extended period at its plant in Coventry, UK. Supplied by nearby automation supplier and KUKA Robotics subsidiary DV Automation of Birmingham, it is used to hem bonnets and tailgates for UK automotive customers.
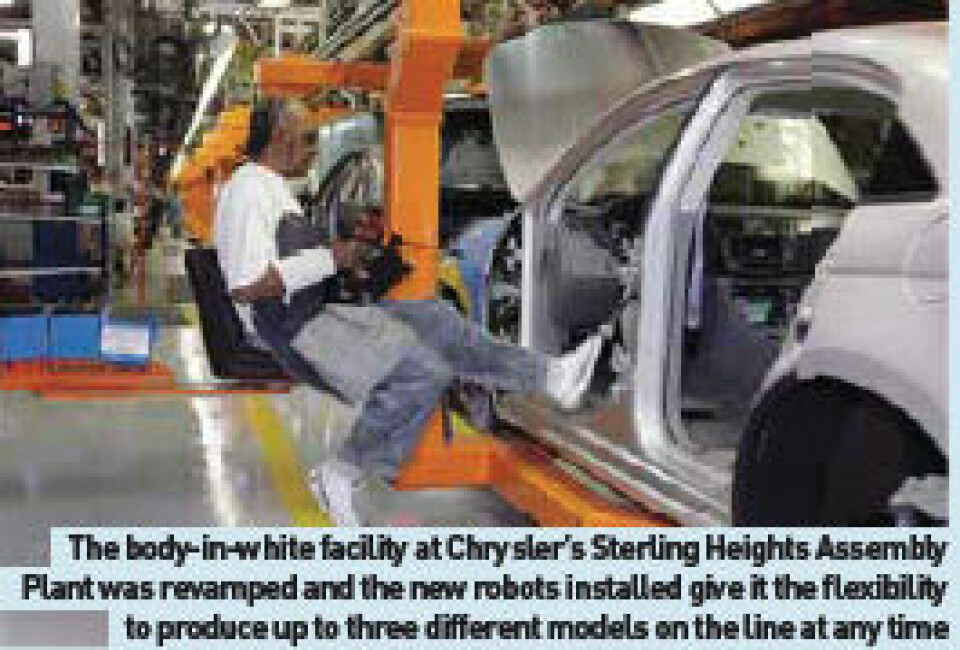
The cell comprises a single hemming station positioned around a Kuka KR150 robot equipped with a roller hemming head. The robot guides the hemming head around the part to form the hem join, ensuring that the inner and outer panels of the component are properly closed to form a safety edge. The cell has been designed to handle a number of model variants and is capable of expansion to perform other tasks. In fact, Stadco is already considering extending the cell’s capabilities so it can operate dispensing equipment for sealant application.
According to Mark Schlanker, Business Manager for DV Automation, the installation reflects the increasing demand from automotive sector customers for intrinsic flexibility and easy re-use of automated manufacturing systems. He says that the demand for such re-usability is now routine: “Carmakers simply don’t want to scrap existing production facilities when they introduce new models,” he explains. The demand can be retrospective as well as applicable to new installations. According to Schlanker, a major (unnamed) OEM recently approached DV Automation to find a way to enable the retooling of a five-year old hemming cell for a new vehicle in a maximum of just two days.
Regarding new installations, Schlanker indicates that he expects a requirement for formal proof of re-usability to become an integral part of the tendering process. In terms of the robot itself, this will require a combination of reprogrammability with ease of retooling, neither of which are in themselves unprecedented. After all, reprogrammability is part of the official definition of a robot. One consequence, he believes, could be a greatly enhanced importance for simulation systems that can demonstrate the efficient operation of a manufacturing cell even before it is commissioned. It is quite feasible that alternative configurations of the same equipment might also have to be proved out as part of the sales process. Stadco’s use of robotic hemming is already set for a major expansion. It is currently setting up a new body-in-white facility in Russia, approximately 20 kilometres from St Petersburg, to serve OEM plants and various carmakers in the region. An important part of the plant is robotic hemming, capable of producing the chassis closures for up to 100,000 vehicles a year. The plant, which is scheduled to open at the end of 2008, is a joint venture with Spanish company Gestamp.
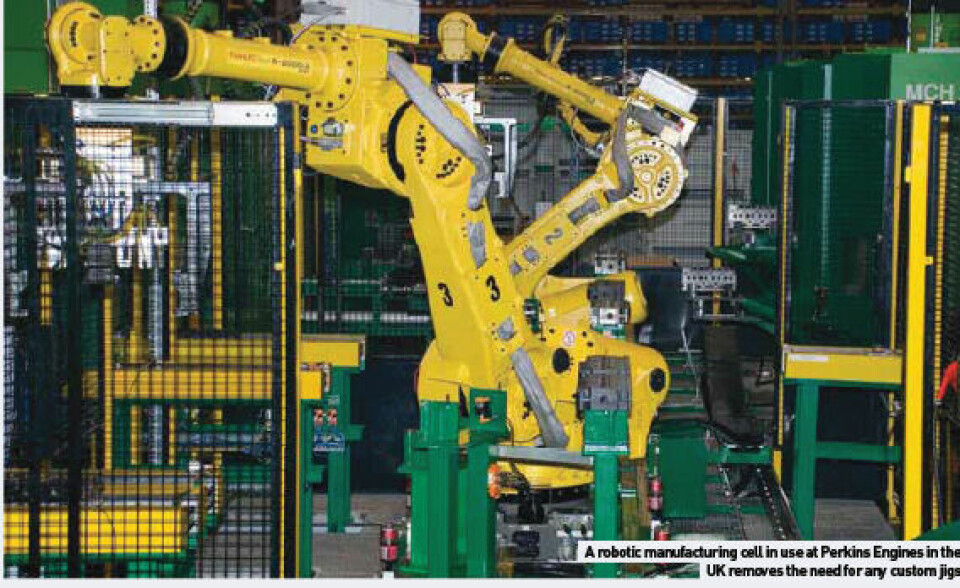
The predominant robot supplier is ABB Robotics. ABB has said that the hemming facility will comprise 14 robots, representing an investment of around US$5 million. Production testing is due to take place this autumn in France. The installation will then be disassembled and transported to St Petersburg. Stadco’s facility will use ABB’s IRC5 robot controllers, capable of controlling up to four robots simultaneously, further compressing cycle times. For his part, Meeson has several other observations on how robot applications are developing in the sector. There is, for example, a growing use of ‘coordinating robots’, in other words, two robots working together to make what is a single machine with two arms.
Although not at liberty to say where, he recalls seeing an installation where two robots worked together to pick up a side of a van. What he does say, though, is that a combination such as this could easily realise a saving on initial capital investment of as much as 20 to 25 per cent over a hard automation alternative. The key technical developments that make this possible are not physical robot structure, but advances in control architecture. The use of controllers with a multiple-robot capability at the forthcoming plant in St Petersburg is an example.
Developments in welding
Meeson also expects to see further developments in one of the most firmly established robot applications – welding. Specifically, he says that the concept of ‘remote laser welding’ is coming closer to fruition. This is a simple enough concept: a laser welding head is positioned as much as a metre from the work piece, as opposed to the extremely close range that is the norm now, but the implications are considerable. “Because the welding head is so far back from the work piece, it can be relocated from one weld point to the next extremely quickly. Only a small movement of the head is necessary to achieve an extremely wide traverse,” he explains.
The technology is not yet a reality, but Meeson says that Stadco has laboratory trials under way and the company is optimistic a practical system could be developed for real industrial use within two years. The rewards could be considerable, the overall increase in operational efficiency translating into cost reductions by as much as thirty per cent per weld, compared with today’s counterparts, according to Meeson.
Girish Nadkarni, Head of Automotive Business (Worldwide) for ABB Robotics, points out that the industry is far from homogenous. He says that the new or heavily re-equipped carmaking plants now appearing in the emerging economies of the former Soviet states, India and parts of the Far East (most obviously China), have some subtly different requirements to those in the US, Europe and Japan.
“It really isn’t just one huge industry,” he says. The demands of those markets are highly influential in driving developments in human-machine interfaces (HMIs) that can make robots easier to program. The older Western approach, in which carmakers were routinely able to employ several software engineers to do complex programming routines, is simply not feasible in such places. As far as the company’s more established markets are concerned, Nadkarni says there is an increasing demand for robots that can replace single-purpose manufacturing installations, replacing them with something more versatile. “The emphasis in the developed world has shifted away from simplicity and cost reduction to flexibility and reusability,” he states. Indeed, reuse of robots, which was simply not a concern of any significance a few years ago is, according to Nadkarni, “now a major issue for western OEMs.”
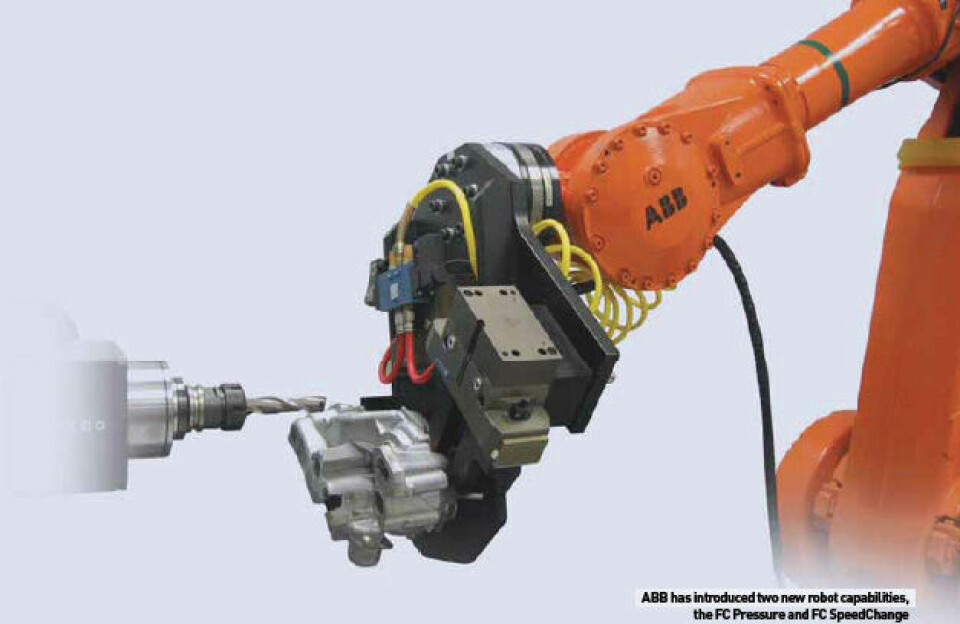
Reprogrammable robotic devices
ABB has responded to the push for reusability by introducing a concept termed FlexLean. This is essentially an approach to robotic cell design built around the principles of modularity and the use of reprogrammable robotic devices to replace ‘hard’ fixturing. For instance, a small robot with just three axes of movement can be used as a positioner to support a car body or other work piece, where previously a dedicated jig would have been required.
Similarly, a highly flexible gripper, appropriately named FlexGrip, can be programmed to carry out different gripping operations and in some cases, entirely remove the need for a robot to change tools for manipulating different items on the production line. Nadkarni says that the concept, which was introduced 18 months ago, is making headway in the industry and is now being used by half a dozen automotive firms in the US, Europe, India and China. He claims this is the start of the changeover from “one hundred per cent hard tooling to one hundred per cent robotic tooling”. In the past year, ABB has introduced two more robotic capabilities – the FC Pressure and FC SpeedChange. The first allows robots to carry out grinding, polishing and buffing operations while maintaining a constant pressure between the tool and the work surface. In effect, it allows a robot to ‘feel’ what it is doing. The second facilitates robot deburring and deflashing operations by allowing speed changes according to the resistance encountered by the tool. Both capabilities illustrate Nadkarni’s observation that it is software and control technology rather than hardware configuration that will be the real drivers of robotic innovation in the near future.
Nadkarni discounts any idea that the robots will be reduced to just a few basic, generic units, capable of near limitless adaptation. There are a number of basic performance factors that, by definition, have to be highly variable to enable robots to be fit-for-purpose without being needlessly over-specified. Most obviously, he points out, these include reach, working envelope, lifting power, accuracy and stiffness.
To satisfy the different combinations of these capabilities needed by different customers requires the company to offer around a dozen basic robot types, with several variants within each range, and he does not envisage this situation changing significantly in the foreseeable future. Further ahead, though, all sorts of possibilities loom. In the longer term, Nadkarni suspects the trend will be toward the further development of ‘human-like’ capabilities. Many of the basics are already present in some form – robotic vision and synthetic ‘touch’, for instance – though he says that in developed countries with ageing populations, Japan most obviously, there is increasing interest in the prospect of ‘humanoid robots’ as replacements for shopfloor workers.
Chrysler’s Sterling Heights Assembly Plant in Michigan, US, was extensively remodelled in early 2006 as part of a $500m investment that also involved development of a separate stamping plant which effectively acts as Tier One supplier to the assembly operation. In the assembly plant, the bulk of the investment was used to revamp the body-in-white operation that now features about 620 robots. This arrangement allows production of up to three different models on the line at any one time, with the added flexibility of proving out the production processes for another model at weekends. The degree of interchangeability between models is total, meaning that the line can be dedicated to producing just one model, or any combination of the three.
Clean sweep
Robert Barstead is Director in Advanced Manufacturing Engineering for Chrysler, based at the company’s world headquarters and technical centre in Auburn Hills, north of Detroit. He says that all the robots in the BIW facility were sourced new for the project and were provided by three different vendors – ABB, Fanuc and Nachi. There were robots previously, but they could not provide the degree of flexibility that Chrysler required. The whole facility, as Barstead explains, was “gutted, after which we installed a new framing and closure assembly process”, though some ancillary equipment, such as conveyors, was re-used.
The line is now capable of building four unique upper bodies and three unique underbodies, though in practice the latter capability is not fully exploited. Barstead says that the robots (by total number) are approximately split 60:30:10 for welding, materials handling and other applications such as measurement. Currently the line produces the Dodge Avenger, Chrysler Sebring and Sebring Convertible, with the line having previously piloted the Jeep Patriot, while the Dodge Caliber and Jeep Compass were on the line together, as were the Dodge Challenger, Chrysler 300 and Dodge Charger.
Barstead explains that Sterling Heights is not a pioneer in this approach within the Chrysler group; the company’s plant in Belvidere, Illinois, having led the way in 2006 – but the lessons learned from that programme have been rolled out across the carmaker’s North American operations.
Surprisingly, he says that despite the plant’s innovative use of robotics, it was not necessary to introduce any new ways of working with the robot’s suppliers. “There wasn’t really what you would call a collaborative approach,” he says. Instead, Chrysler communicated its requirements to a single integrator, in this case the robot systems provider Comau, despite the company not supplying any of its own equipment. “It was a process carried out by the integrator to our specification.”
Total flexibility
According to Barstead, the changeover to an almost entirely robotic approach was facilitated by several factors – increases in payload capacities, accuracy and flexibility, but most importantly, cost. Prices of robots have decreased sharply in recent years and Barstead believes a comparable facility equipped with more infl xible, hard automation would have cost twice as much.
As it is, the set-up has cancelled the need for such products as a dedicated lift-and-carry transfer system, and supplementary equipment such as turntables, although the underbody assembly still needs a specific underbody pallet. The advantage for Chrysler is the flexibility of production; there are no quality implications. “It doesn’t have an impact, either positively or negatively, on product quality,” he confi rms. Instead, the carmaker now has an enhanced ability to respond to market fluctuations. It can switch production between models more or less at will. Even switching to a completely new model presents few problems. Barstead is almost dismissive on the point: “If I want to add a new vehicle, I just have to add end-of-arm tooling. I don’t have to buy any new robots.” Actual reconfi guration of the facility would only be necessary if the vehicle’s architecture was fundamentally different – most obviously if it was a truck and not a car.
In current day-to-day operations, the plant outputs 72 vehicles per hour, with a minimum batch of 20. A reasonably normal pattern of production would run at 100 Avengers, followed by 100 Sebrings and then 20 Convertibles, though, as Barstead notes, if a burst of warm weather caused a sudden jump in demand for soft tops, the company could respond to the demand. That, ultimately, is the whole point of the investment.
Close co-operation between user and supplier
A robotic manufacturing cell commissioned last year by Perkins Engines of Peterborough, UK provides an interesting example of close cooperation between user and technology suppliers. A diesel engine manufacturer, the £5m cell makes some 80,000 of the company’s Type 400 D cylinder heads each year. Previously outsourced, the production was brought back in-house after an internal project team benchmarked the benefits of continued external sourcing versus own manufacturing. The team selected two suppliers of automation technology, robot supplier Fanuc and machine tool manufacturer Heller, to be active partners in the venture, selected on the basis of several key factors, including previous association with Perkins, recorded service and support levels and their existing infrastructures in the UK.
“We asked them to tell us what would be required to make the units cost-effectively and to the required quality levels,” says Tony Green, Manufacturing Coach with Perkins. The outline scheme suggested by Fanuc and Heller was then remodelled by Perkins’s engineering personnel to achieve a final configuration. In operation, pallets of cylinder heads are delivered first to a Fanuc R2000iA/165 robot equipped with a V500iA/3DL vision system that identifies the position of the heads and then selects them using a magnetic gripper. The cylinder heads are re-orientated as needed, given an identification mark and then placed onto the cell’s input conveyor system.
That apparently straightforward pick-and-place sequence contains elements that underline the flexibility that is driving recently adopted robot technology. The use of robotic vision, for example, does more than just allow the unstaffed loading of the cell. It also facilitates the use of standard pallets and, crucially, removes any requirement for custom jigs. The robot is used again at the end of the machining cycle to load machined heads into a leak-testing machine, then returned to a pallet.
Inside the cell, the six machining centres are serviced by two of Fanuc’s R2000iA/165 robots, each of which is capable of servicing the entire cell independently, ensuring continued operation even if one robot malfunctions. Yet before the cell went into operation, several of Perkins’s personnel were seconded to Fanuc’s and Heller’s UK sites to familiarise themselves with the equipment involved. Green says that the success of the installation is derived in part from Perkins’s recognition that, especially with such sophisticated technology, the supplier-customer relationship works both ways.