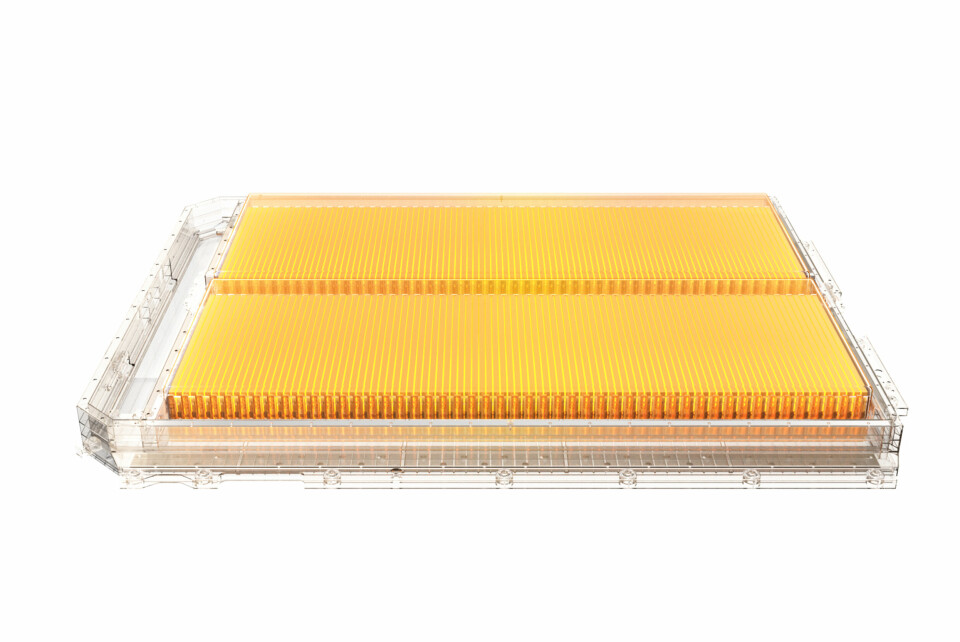
EV battery testing – new software supports testing rapidly changing battery technologies
New battery technology is being developed, and testing companies are focused on the same old parameters. But change could be on the horizon with new software.
Battery technology for EVs is constantly evolving. New chemistries are being developed, and existing systems are becoming increasingly efficient. Could these changes potentially have an impact on how batteries are being tested, the parameters considered, and the level of detail that is required?
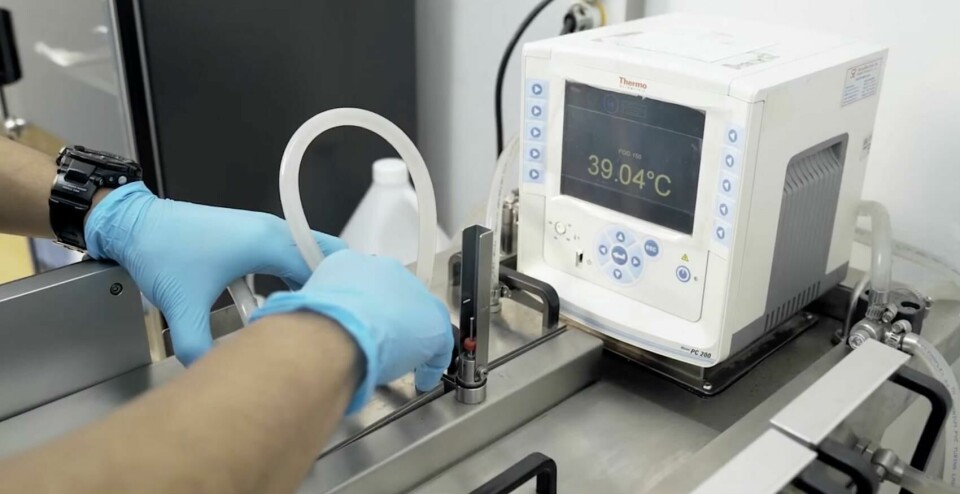
Back to basics
Zeekr, an EV-only subsidiary of Chinese OEM Geely, has recently revealed details of the latest upgrade to its lithium iron phosphate (LFP) prismatic batteries. The company says that the batteries support 5.5C ultra-fast charging and can be charged from 10% to 80% in 10.5 seconds, making it the quickest charging EV battery pack in the world.
BYD and CATL are reportedly working on LFP battery technology, as is LG Energy Solutions. The latter, which provides batteries for the Tesla Model 3 and Model Y, has also said it will soon launch its new 4680-type cylindrical battery cells. Other companies including LG, SK On and Samsung are also examining the development of prismatic batteries.
The above examples are just a small sample of the many advancements recently made and currently on-going in battery technology. But, despite this constant evolution, Stefan Menacher, Site Manager, Garching, TÜV SÜD Battery Testing, suggests that little has changed when it comes to testing batteries.
“The general idea of testing is still the same as it was ten years ago,” he notes. “We want to ensure that our customers get reliable and, above all, safe products. Of course, procedures have been refined and standards have been developed. The amount of energy stored in a battery has also increased many times over, but the basics for battery testing are still the same.”
BEV battery testing started at TÜV SÜD in 2012, when the company established a joint venture with Lionsmart to form TÜV SÜD Battery Testing. A testing laboratory was built near the German city of Munich, and subsequent years of expansion led to new laboratories in North America and Asia. The company mainly tests lithium-ion batteries for BEVs, but also carries out testing work for industrial and medical applications.
“We can actually test all kinds of batteries, from a small battery for a medical device to systems for road vehicles and even stationary containers for electrical grid stabilisation,” Menacher continues. “Within this portfolio, we can perform all kinds of tests, for lifetime and durability, environmental impact tests and, of course, safety tests.”
Delving into these parameters, and it quickly becomes clear that there are a myriad of separate issues that must be considered. In the safety tests, for example, the battery must perform without overcharging or short-circuiting but must also be tested for fire resistance and crush resistance. The safety and reliability of batteries must also be tested when subjected to a variety of extreme conditions, in different temperatures and humidities.
“One of the big problems that arises with BEVs is that from an integration and software standpoint, all the different systems have a much more complex interaction than in the conventional propulsion systems”
Matthias Dank, AVL
Complex interactions
As well as considering many different issues and parameters, testers must also be aware of the interaction that the battery has with the numerous systems in the vehicle. Many of these interactions could have an impact on aspects such as battery life and performance and may also subsequently have an impact on other parts of the vehicle like the motor.
“One of the big problems that arises with BEVs is that from an integration and software standpoint, all the different systems have a much more complex interaction than in the conventional propulsion systems,” says Matthias Dank, board member and executive vice president at AVL. “If something else is draining power from the battery at the same time, then there are implications for how the motor might perform, for example.”
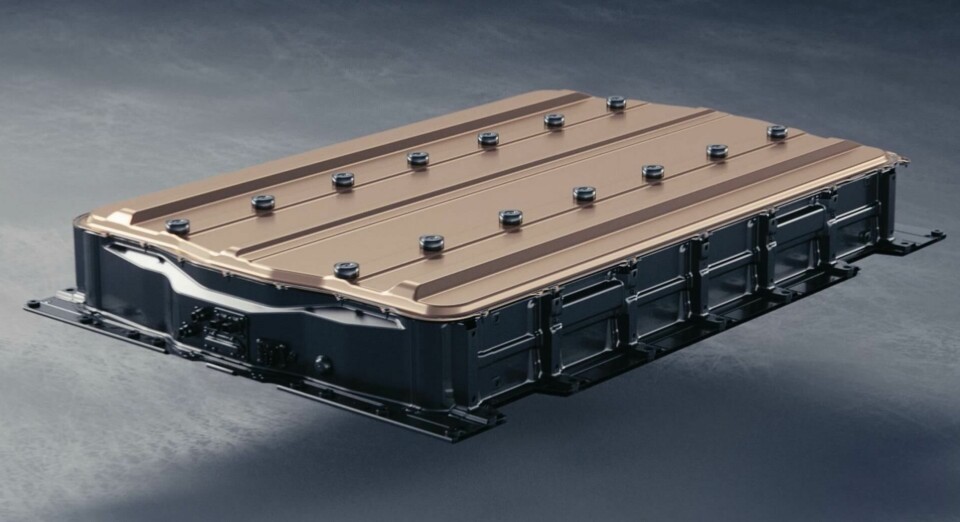
With the digitalisation of vehicles, increasing connectivity and software capability, and autonomous driving functionality, these interactions are becoming increasingly complex and intertwined. Dank suggests that the battery will play a pivotal role, and that testing will need to include more areas of the vehicle.
Menacher also acknowledges the fact that systems are becoming more complex as new components and functions are introduced. He refers to the ability that some new vehicles have, like the GMC Hummer EV and Chevrolet Silverado EV, to switch between 400V and 800V systems. The switch allows drivers to charge these vehicles faster by temporarily connecting the dual battery packs together. This means that testing must be done on the battery packs individually as well as when they are working in tandem.
However, when it comes to the digitalisation and autonomous driving, Menacher does not believe BEV battery testing will change a great deal. “I don’t think that digitality and interfaces have any impact on physical battery testing,” he asserts. “The system has to be reliable, no matter who or what is pushing the accelerator or using the steering wheel. Regardless of whether there is a battery and motor or a combustion engine, we always need to carry out all the necessary safety tests. Things that interact with each other might also affect each other, but in the case of safety tests, this effect is small because the basic functions must be performed no matter how many parts are attached. It’s the same as with the sockets in your home.”
“Each system is unique, and we have to integrate them in our test structure because we also have to communicate with the batteries in a way that pretends, they are in the car and working as designated”
Stefan Menacher, TÜV SÜD Battery Testing
Compatibility challenges
But the detail or complexity of parameters is not the most difficult part of BEV battery testing. According to Menacher, the most challenging role of the battery tester is ensuring every battery is compatible with the testing equipment. This can be particularly tricky when attempting to obtain test results that closely represent how the battery will perform under real-world conditions.
“Each system is unique, and we have to integrate them in our test structure because we also have to communicate with the batteries in a way that pretends, they are in the car and working as designated,” he confirms. “This step is quite complex, and it always takes some time to commission the batteries on our test benches.”
BEV battery testing is application-driven, as the cells and modules need to be tested in a way that is true to how the EV would be used by a driver. However, shipping finished vehicles off to battery testing companies would quickly become very expensive and time consuming for carmakers and battery manufacturers. Battery testing equipment reconfigurations must, therefore, mimic different applications and comply with battery product changes. This typically requires a significant capital investment not only in EV battery testing equipment but also in the integration of the different testing fixtures to support the changes.
Furthermore, each project for BEV battery testing is different, Menacher clarifies. He and his team may be working with a carmaker or, in some cases, directly with a battery manufacturer. This does not alter the testing parameters, nor the level of detail in which the testing must be carried out. However, it may change the time at which companies like TÜV SÜD become involved.
“We have accompanied batteries from the first hand-made sample to fully automated production and approval for use on the road,” he clarifies. “It just depends on how the project is set up, and we must be flexible and cater to each customer and their needs.”
Like Menacher, Dank suggests that it is beneficial to have a testing company involved at the early stages of battery development: “The typical way to check how each system performs when interacting in a real-world environment is to test a real car on a real road. But that is the costliest test environment and too late in the development cycle. So, the question becomes: what is the right environment to develop the systems and identify problems at the earliest stage?”
No battery, no problem
BEV battery testers already simulate many parts of the vehicle with the goal of providing data that is as accurate as possible without needing to use the whole vehicle for tests. One company is taking it a step further and has abandoned the battery altogether.
NI – a provider of software-connected automated test and measurement systems owned by parent company Emerson – offers battery emulators for testing purposes. The company argues that using real batteries requires time-consuming processes like charging, discharging, and letting the battery rest to bring it to a test appropriate state of charge (SOC). When using battery emulation, all this preparation is significantly reduced because the battery emulator immediately provides the realistic battery characteristics needed, which helps engineers focus on tests instead of battery behaviour nuances.
The use of battery emulators could also alleviate the challenges that Menacher and Dank listed, such as the compatibility of batteries with testing equipment and the exclusion of battery testing companies until the last moments of product development. However, both Dank and Menacher believe that the physical testing of real batteries will remain crucial as the BEV market grows. Simulations and emulators could play a certain role, perhaps when considering non-critical parameters. But when it comes to meeting industry standards and regulations, the testing of real batteries will not be replaced in the near future, especially when new battery chemistries and structures are being developed and are hitting the market for the first time.