Korea’s LG, SK On and Samsung lead Prismatic battery revival impacting Electric Vehicles and Automotive Production
The prismatic battery is making a comeback, with Korean battery giants leading the charge. Offering advantages in safety and cost, this technology could have lasting implications for the Electric Vehicle, battery, and automotive production landscape.
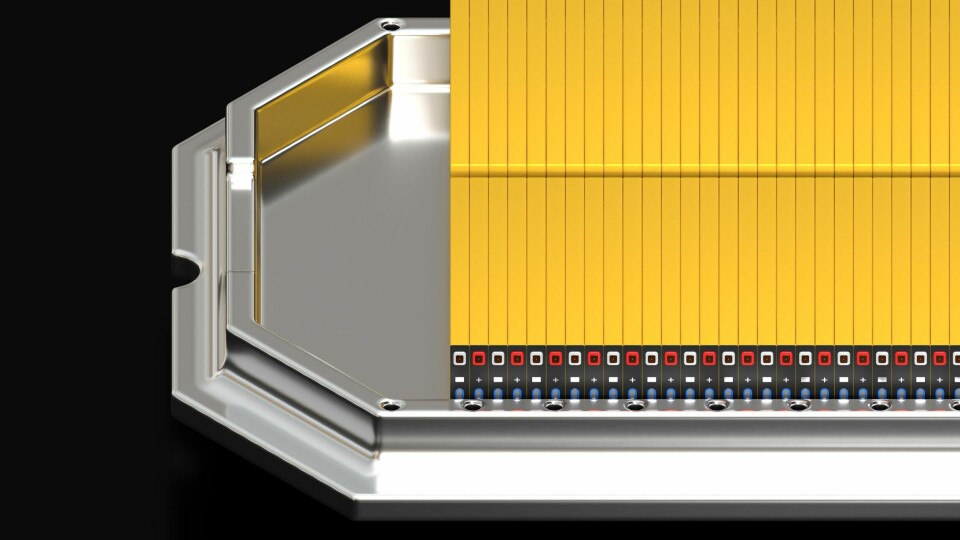
South Korea’s battery and technology behemoths are making a strategic pivot towards prismatic batteries, a technology experiencing a renaissance in the electric vehicle (EV) market. This refocusing could signify a potential shift in standards within the global battery landscape, driven by a confluence of safety concerns, cost considerations, and evolving design preferences. LG Energy Solution, an industry leader, is spearheading this movement by forming a task force dedicated to the mass production of prismatic batteries. If LG successfully navigates this transition, it will become the first company to offer all three major battery form factors – pouch, cylindrical, and prismatic – potentially securing a significant competitive edge.
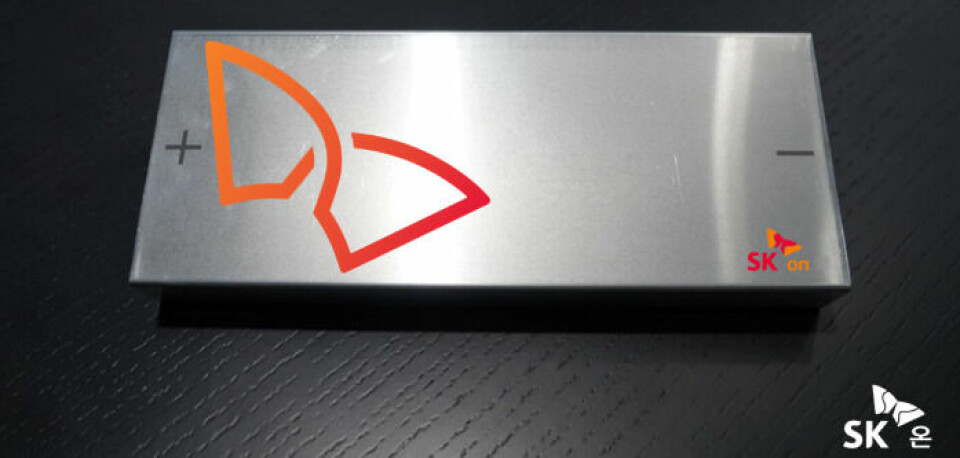
The prismatic architecture resurgence
This resurgence comes after a period of relative dormancy for prismatic batteries, which were initially developed by LG itself in the 1990s.
However, market research from SNE Research paints a compelling picture: prismatic batteries captured a staggering 49% share of the European market in 2023, a dramatic rise from 19% in 2019. This surge eclipses the market share of pouch (35%) and cylindrical (16%) batteries in the same year.
The benefits of Prismatic Batteries for Automotive Manufacturing
The growing allure of prismatic batteries for automotive production stems from several key strengths. Their robust aluminium casing translates to enhanced resistance against external shocks and improved durability. They also boast robust safety features like pressure-relief vents and current-limiting fuses, mitigating the risk of thermal runaway – a critical concern for EV manufacturers.
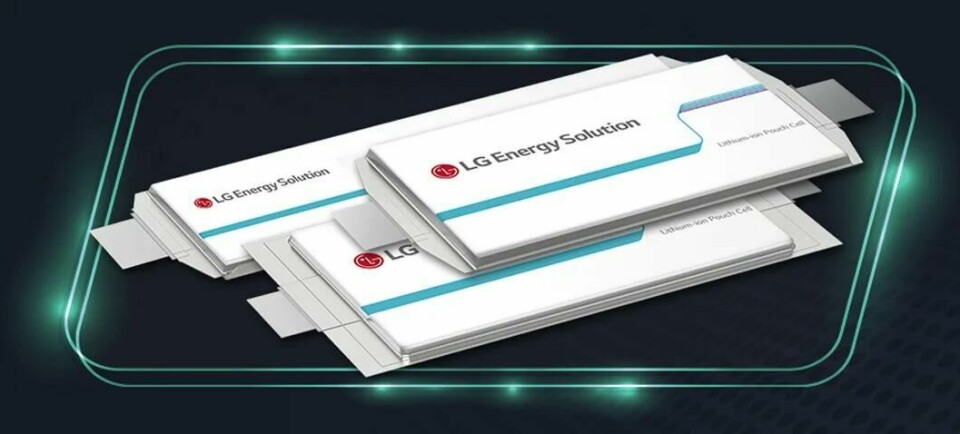
Additionally, the wide base of prismatic batteries allows for optimal heat dissipation through increased contact with the cooling plate.
While they might be slightly heavier and possess lower energy density compared to their pouch and cylindrical counterparts, prismatic batteries offer a compelling counterpoint: cost-effectiveness.
Simpler production processes and lower manufacturing costs make them ideal for mass production. Furthermore, their ability to be directly mounted without additional safety measures makes them well-suited for cell-to-pack (CTP) configurations, a design philosophy gaining traction in the industry.
This recalibration towards prismatic batteries is further solidified by their increasing adoption by major automakers. The German giant Volkswagen exemplifies this trend, with plans to integrate prismatic batteries in 80% of its EV production by 2030.
As cost optimisation and safety concerns remain paramount, prismatic batteries, with their unique blend of strengths, could redefine the future of electric mobility.