How Ford’s Marc Dugas is supercharging battery pack assembly using the POSIWID system
In this Q&A we explore how Marc Dugas, Ford’s Technical Specialist for Battery Pack assembly, uses a little-known systems thinking heuristic called POSIWID, (the Purpose Of the System Is What It Does) to supercharge battery pack assembly
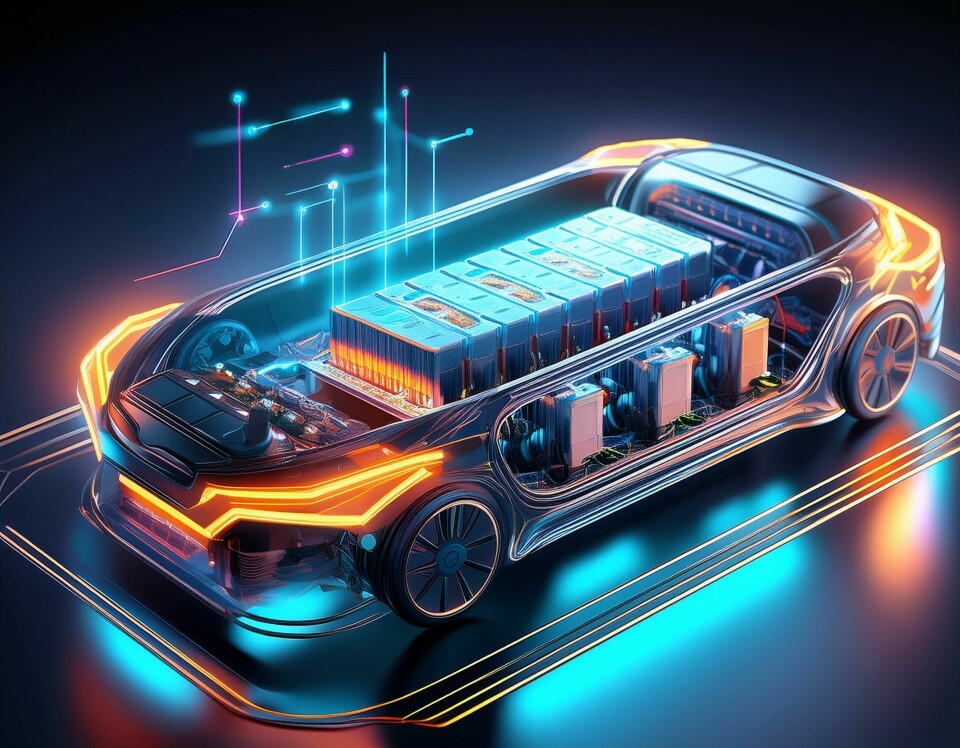
What does it mean for battery pack assembly to hold, ”the Purpose Of the System Is What It Does”?
Systems of thinking, and models of conceptualisation, are primary to the material systems themselves. This is no ideal. So in the quest to reimagine and reformulate battery pack assembly at Ford, the POSIWID approach offers a transformative lens.
The methodology emphasises a systematic and humanistic mode of thought and communication, beginning with an expectation. In the battery assembly realm, it asks a fundamental question: “What should the system be doing?” This approach bypasses the immediate pressures to find solutions, allowing for a clear delineation of expectations unburdened by current system limitations or team pressures.
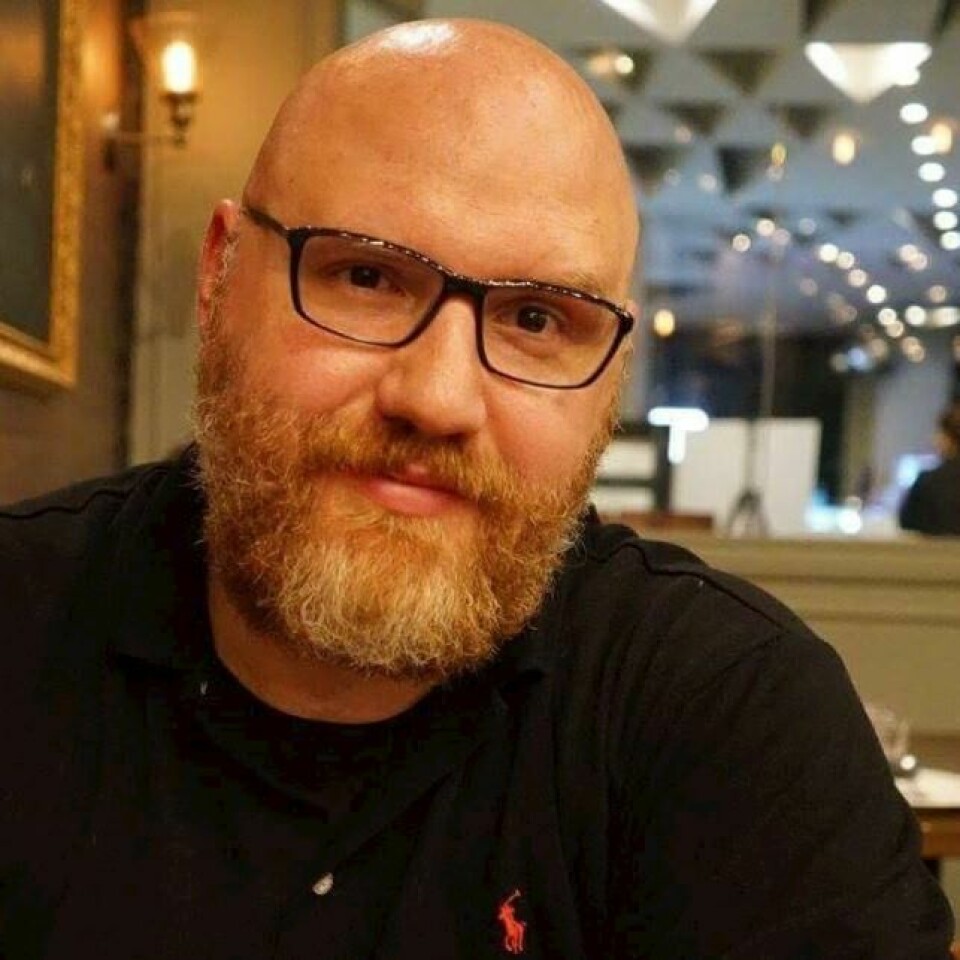
As Marc Dugas applies this heuristic to innovate battery pack assembly processes at Ford, the focus remains on fostering collaboration between design and manufacturing teams, leveraging digital twins for real-time accuracy, and reducing non-value-added engineering time through standardised communication and digital tools.
The meticulous approach ensures that every step towards innovation is deliberate, measurable and aligned with overarching expectations for battery pack innovations.
“Production efficiency is about deleting components and processes. Regardless of the cell chemistry, working toward component reduction initiatives is a promising development”
Marc Dugas, Battery Pack Assembly Specialist at Ford
How are you applying the POSIWID approach to innovate on battery pack assembly processes at Ford?
The questions developed for analysing everything regarding POSIWID are a systematic and humanistic way of thinking and communicating; POSIWID starts with an expectation. What should the system be doing? You don’t need to start with a solution; you need to start with an expectation. The expectation is what the system should be doing and does not contain inputs of what the system is actually doing. Therefore, the expectations do not need to be tamped down by the current limitation of the system or the pressure from the team to talk directly about solutions rather than expectations.
The solutions or actions to close the gaps to the expectations come later in the process. We may not know where we are going, but at least we know the expectations to fill when we arrive.
As you work on future battery pack technologies at Ford, what are the most promising developments for improving EV battery efficiency and production?
Production efficiency is about deleting components and processes. Regardless of the cell chemistry, working toward component reduction initiatives is a promising development that provides value to end users. Customers want their expectations achieved, not for us to offer well-designed brackets.
And how are you balancing the need for rapid innovation in battery technology with the requirements for scalable, efficient manufacturing processes?
Design for manufacturing must be considered from the start of a product design and be a key input to all the components selected. Collaboration between design and manufacturing teams must be early in the design process, and there must be effective feedback loops between the manufacturing and product development teams. Efficient use of current tools may be feasible if the right two people are talking together in a workspace.
“Standardising communication in the form of POSIWID and clearly defining expectations reduces non-value-added engineering efforts”
Marc Dugas, Battery Pack Assembly Specialist at Ford
What are the key challenges you’ve encountered in transitioning from engine assembly to battery pack assembly, and how are you addressing them?
Training people on Geometric Dimensioning and Tolerance (GD&T). The scale and manufacturing variability of the components prevents many of the pre-planned motions that traditional automation requires. There are a few new processes to learn and add to the toolbox, but many of the processes, in their fundamental nature, don’t change: fixture, Pick, Place, Fasten, Dispense and Test. Learning a new set of expectations from the result of the process requires a lot more meetings than it used to.
How are you leveraging digital twins to improve the integration between engineering and manufacturing in battery production?
Collaboration between engineering and manufacturing has greatly benefited by creating single points of truth that are always accurate in real-time. Creating feedback loops in the context of the digital twin reduces engineering hours spent creating PowerPoint presentations trying to explain something offline.
Can you elaborate on some specific strategies you’re implementing to reduce non-value added engineering time in battery production?
Standardising communication in the form of POSIWID and clearly defining expectations reduces non-value-added engineering efforts. All stakeholders can align around a functional expectation rather than an inference of function through a possibly misguided specification. Tell me the specifications and the expectations you are trying to achieve, and then we can collaboratively discover the gaps in the expectations early in the process.
Utilising digital tools that create collaborative spaces with a single point of truth is crucial in eliminating non-value-added engineering time. Designing a process for a PowerPoint or Excel file that resides on a single person’s hard drive and takes weeks to update a change into is not a value-added process.
With your focus on design for manufacturing and assembly, what innovations have you introduced to streamline the battery pack production process?
I’ve been listed as an inventor or co-inventor on 21 published patents in the traction battery field. Most of the patents concern the assembly process of prismatic cell battery packs. In terms of design for manufacturing, we focused on eliminating the number of components required to assemble the pack. I’m currently focused on robust solutions for tool-centre-point automated setup and challenge processes.