Solving EV battery pack development, cost and production challenges
James Eaton, CEO of IONETIC, discusses the evolving landscape of EV battery pack development and production, focusing on the challenges facing low-volume manufacturers. Eaton shares insights into the importance of cost optimisation, flexible manufacturing, and overcoming the unique challenges of electrifying commercial vehicles such as buses.
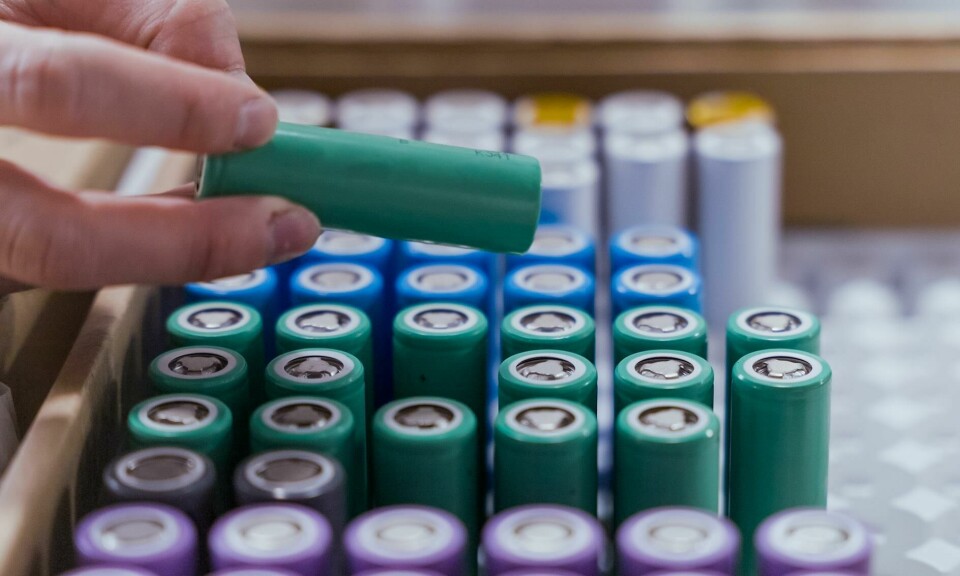
As the transition from internal combustion engines to electric powertrains accelerates, the development of EV battery packs remains a key challenge for many manufacturers, particularly those in the low-volume segment such as heavy commercial vehicles.
“Most low-volume OEMs cannot afford the traditional way of electrifying. You either develop a custom solution at a high cost, or you opt for something off-the-shelf, which might not meet your specific needs”
James Eaton , IONETIC
Custom battery pack vs off-the-shelf technology
According to Eaton, the traditional routes of developing EV batteries often leave smaller players at a disadvantage. He highlights two main approaches available to OEMs today: investing heavily in custom battery pack development, which can cost upwards of $30m, or settling for an off-the-shelf solution that can compromise performance and size.
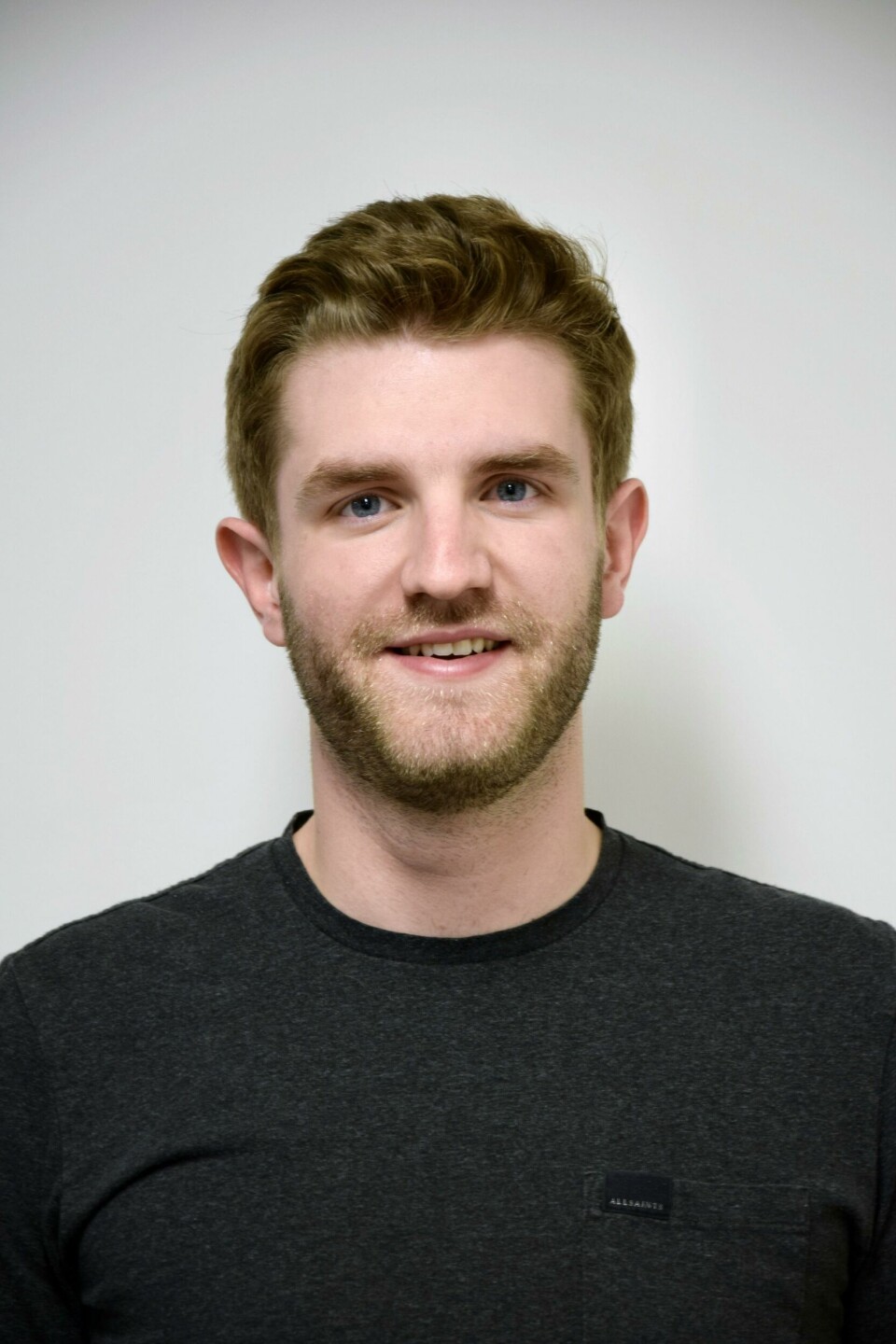
“Most low-volume OEMs cannot afford the traditional way of electrifying,” says Eaton. “You either develop a custom solution at a high cost, or you opt for something off-the-shelf, which might not meet your specific needs.”
For low-volume manufacturers, the barriers to developing EV battery packs are not limited to cost alone. Speed to market and risk management are equally critical. Eaton points out that many manufacturers, especially those producing fewer than 10,000 vehicles annually, find the timelines and risks involved in developing battery technology to be daunting.
However, Eaton notes that with the right approach, OEMs can reap the benefits of using battery powertrain technology that is already validated, but can be correctly matched to meet the performance, packaging and cost requirements of the vehicle manufacturer with a reduced timescale and cost. This is an approach that has been further developed by IONETIC.
Electrifying buses: A unique set of challenges
Working on electrifying heavy vehicles, IONETIC’s collaboration with bus manufacturer, Alexander Dennis, offers a glimpse into the unique challenges of electrifying commercial vehicles. According to Eaton, electrifying buses is far more complex than electrifying passenger cars due to the intense duty cycles and long lifespan requirements.
“Electrifying buses is extremely difficult. Unlike passenger cars, buses run every day for up to 20 years, which means their batteries need to last through 7,000 cycles,” Eaton says. In contrast, a typical EV passenger car might only go through around 800 cycles over its lifetime.
This creates a need for bus battery packs that not only deliver high energy density but also ensure long-term durability under challenging conditions. Buses also face weight constraints, as carrying too much energy storage could reduce passenger capacity – a critical consideration for public transport operators aiming to balance performance with operational efficiency.
IONETIC’s involvement in the BESTBUS project with Alexander Dennis, which includes collaboration with Imperial College London, aims to create a bus battery pack that achieves high energy density, is lightweight, and can withstand 20 years of daily use. If successful, the outcomes of this development could have far-reaching implications for the broader commercial vehicle market.
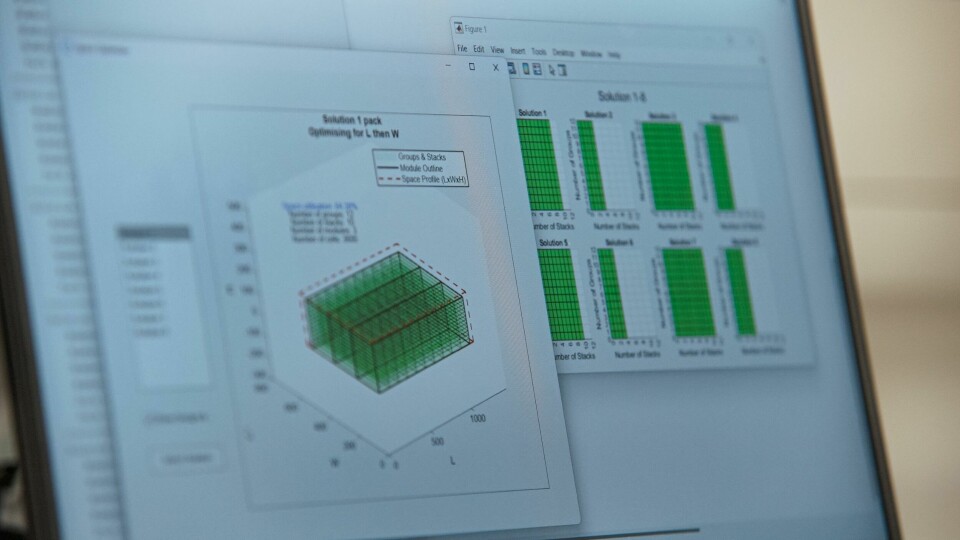
Flexible battery pack manufacturing
“One of the big problems with traditional low-volume manufacturing is that it’s often hand-built, with little automation,” says Eaton. The company has developed its own flexible manufacturing system, which Eaton likens to a semiconductor fabrication plant. Unlike traditional battery production lines, which are designed to produce a single type of battery, Eaton says IONETIC’s system can produce a variety of battery packs without any downtime or tool changes.
The role of AI in battery development
Artificial intelligence (AI) has become a buzzword in many industries, but Eaton stresses that in battery development, AI needs to be used carefully. AI and machine learning, he explains, are most valuable when dealing with multivariate, interdependent problems – complex scenarios where traditional human analysis falls short.
“Battery design is a ten-dimensional problem,” Eaton says. “You can’t solve it with intuition alone.” He highlights how AI can help identify patterns in battery degradation, for example, where multiple factors – such as temperature, power draw, and voltage – can interact in unexpected ways.
However, Eaton cautions that AI must be underpinned by solid physics to avoid false conclusions. “AI will find patterns in the data, but not all patterns are useful. You need to combine AI with a strong understanding of battery physics to get accurate and actionable insights.”