BMW plants prepare for a new era with Neue Klasse production
As BMW gears up production towards its Neue Klasse electric vehicles, the factories are to remain flexible. Gotz Fuchslocher looks at the strategies the manufacturer is pursuing as it prepares to launch production of the new models.
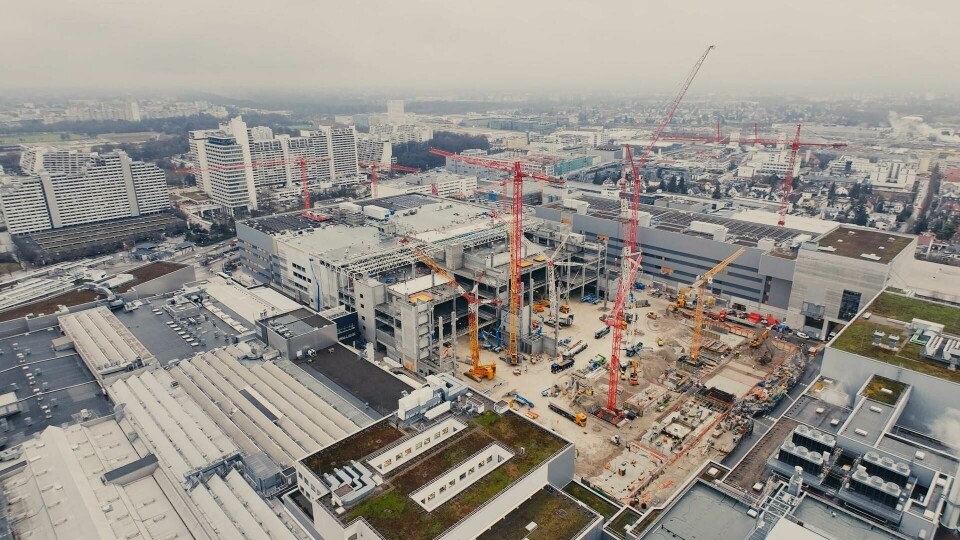
The launch of the Neue Klasse is more than just a new vehicle architecture, it marks the start of an important new era for BMW. And it’s not the first such defining event. Back in the 1960s BMW’s New Class marked a significant change in the way the car was built and in the way the technology was implemented and this approach has supported the company’s success over the intervening years. Now the Munich-based company wants to continue this tradition with the ‘new’ Neue Klasse era.
Constructing a new future for production at Plant Munich
In February this year, the OEM provided the latest insights into this project’s progress at its Munich plant. In addition to the ongoing production of the classic 3 Series and i4 cars in all their drive variants (ICE, PHEV and BEV), the motto of the Munich builders, true to the Peter Fox song from 2008, is “Everything new”.
For the plant, the construction work during ongoing vehicle production represents an immense logistical challenge, due to the constant traffic coming and going. The logistics experts speak of 750 trucks per day for the current vehicle production alone, with an additional 400 trucks per day being added for the construction work. To ease some of the logistical congestion construction of the new bodyshop and assembly hall, (for Neue Klasse production) is utilising prefabricated concrete components – some pieces up to 25 meters long – to save space and reduce the amount of freshly mixed concrete on site. A third new structure will house associated production logistics.
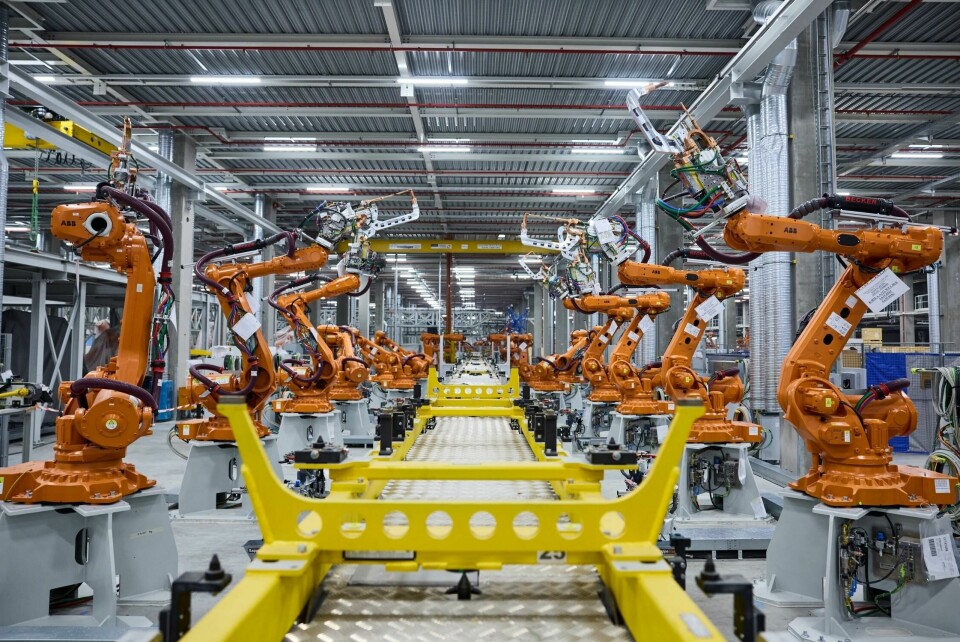
Flexibility contributes to the utilisation of the plants
BMW has been committed to producing mixed powertrain vehicles in its respective plants for years. This so-called exchange flexibility offers the OEM a great deal of security, especially in managing volatile markets. In addition, BMW does not have to deal with vehicle stockpiles and so can react flexibly, especially regarding market demand for electric vehicles.
This means that BMW’s entire production network can produce different model variants and drive types on one line. Production Director Milan Nedeljkovic describes the ramp-up of e-mobility as non-linear, that it is taking place at different speeds. This is why the company is relying on so-called flex plants that can handle both combustion engines and electric drives. The board member emphasises: ” This ensures that we are able to deliver in different market situations and that our locations are fully utilised.”
Neue Klasse production in Mexico and the USA
While BMW believes in the mixed powertrain approach, it expects to see a significant increase in market share for fully electric vehicles. With an eye on electric capacities, the company is not only investing in European greenfield plants such as Debrecen in Hungary and the German brownfield headquarters in Munich, its Spartanburg plant in the USA is also set to produce electric vehicles from the end of 2026, and San Luis Potosi in Mexico is also set to be expanded into another location for the Neue Klasse.
The OEM assumes that by the end of the decade there will be more of a balance between ICE and EVs being sold. On the way there, Munich is setting an example of how to develop from a combustion engine to a flex plant and finally to a plant for electric vehicles, says plant manager Weber, explaining the company’s own strategy . Board member Nedeljkovic points out the 15 electric derivatives that the company currently has in its portfolio. These also ensure compliance with CO2 regulations this year. Nevertheless, the board said that they were sceptical about the politically mandated phase-out of combustion engines by 2035.
We are proud of the know-how, the experience and the desire for improvement of our employees”
Peter Weber, BMW
Neue Klasse aims to reduce manufacturing costs by 10%
The switch to the Neue Klasse also offers advantages in terms of production costs. To this end, board member Nedeljkovic and plant manager Weber zoom in on the production processes, which will be more digital and automated in the future. The two experts speak of targeted automation and complexity reduction. Neither of these should be done at any price. In particular, they must be mastered, says Weber. Innovation must be a means to an end, such as the use of AI in measurement technology, which leads to faster control loops. Nedeljkovic points to streamlined joining processes – mainly spot welding and less exotic processes – less overhead work, quality processes using cameras and AI, and lower paint consumption. All of this adds up to savings in production costs, which according to the board are around 10%.
With the increase in electromobility and the corresponding products in-house, the need for new skills among employees is growing. By flexibly ramping up e-mobility in the plants, they are gradually preparing for new work content, says BMW. ” Despite technical and structural innovations, people are our focus. We are proud of the know-how, the experience and the desire for improvement of our employees,” says Peter Weber. The OEM’s portfolio includes extensive training measures. Last year alone, almost 25,000 training participants were counted in the field of e-mobility. All these building blocks are intended to help the Munich plant survive another change in its eventful history and make a strong contribution to the OEM’s vehicle sales.