Ford Otosan in Kocaeli, Turkey, demonstrates how automation is driving Ford Transit production
The Ford Otosan Plant in Kocaeli, Turkey relies on automation to deal with a very complex number of powertrains and derivatives. Plant Leader, Aysan Hosver, takes us on a tour of one of the most advanced production facilities in the world. With more than 1,200 robots throughout the site, this is how complexity
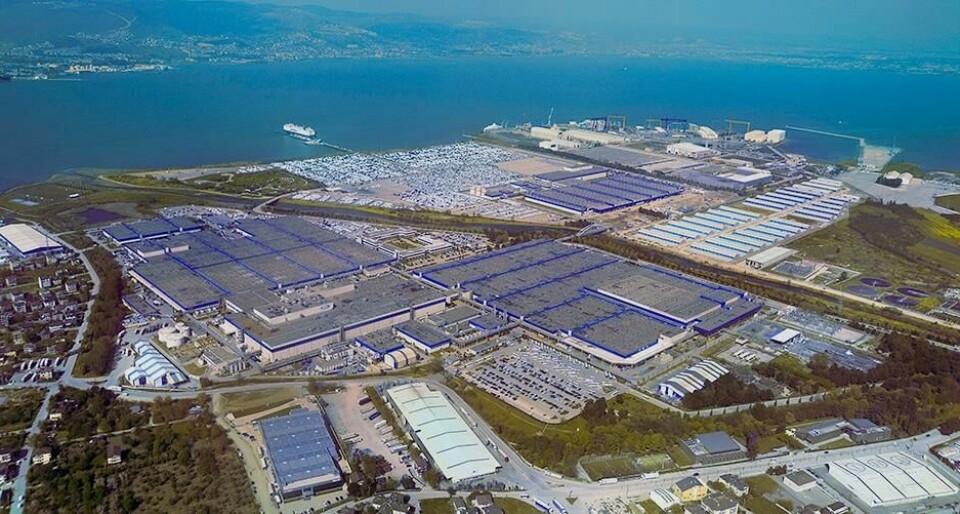
Ford Otosan has invested significantly in upgrading automation and digitalisation for its plants in Turkey to produce the Ford Transit commercial vehicle range. The joint venture between Ford and Koç Group has existed since 1997 but since the latest production centre opened at Kocaeli in 2014, volumes have continued to increase to a point that was not originally intended. At the same time, the Transit has become one of the most complex vehicles to manufacture in Ford’s global production network.
Both the Yeniköy and Gölcük plants on the company’s site at Kocaeli have now benefitted from the upgrades, with Yeniköy set to produce over 405,000 units in 2025. Together they produce 75% of Ford commercial vehicles sold in Europe, including every derivative of the two-tonne Transit and one-tonne Transit Custom ranges.
However, it is the complexity of the derivatives and components that necessitated more automation at the plants.
Increased automation for increased complexity
“There are more than 1,000 types of body-in-white derivatives,” says Aysan Hosver, Plant Leader for Ford Otosan’s Kocaeli site. “Single doors, tailgate, cargo door, no door, van, combi, short wheelbase, long wheelbase, battery-electric, plug-in hybrid electric and internal combustion engines. This level of complexity definitely needs automation, even the Transit parts have derivatives, so employees need to know which part to fit in. There could be 50 or 60 versions of a part.”
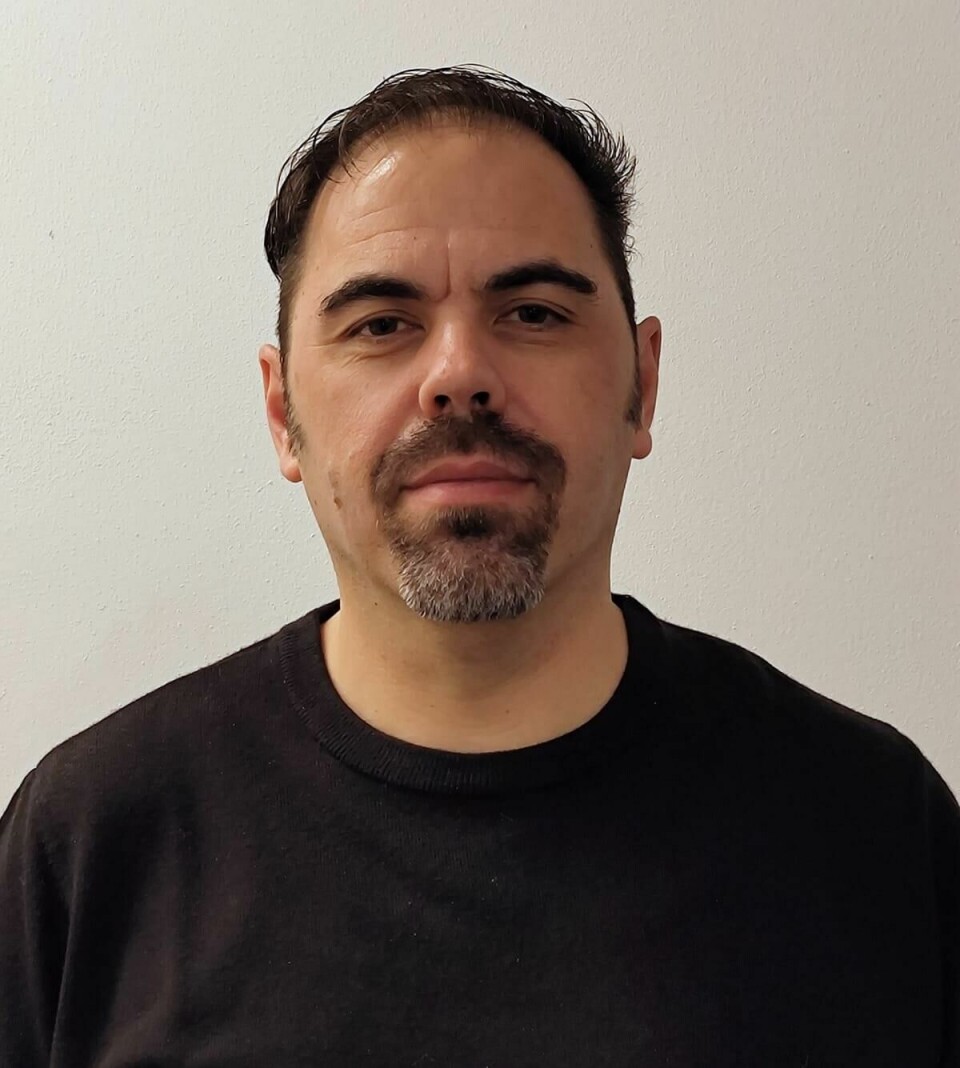
It’s not just about the Blue Oval badge either, because the Kocaeli plants will produce the Transit’s Volkswagen platform sibling, the Transporter and all its derivatives. The total combined production number for both brands is in excess of 405,000. Fortunately, Hosver is able to oversee all of it on a vast digital screen that is the brain of what he calls the Manufacturing Execution System. The screen shows real-time visualisation of the data flow throughout the plants, including production processes, assembly and production lines.
“All of our stations, tools and equipment are integrated on a digital platform where we track the performance of every station,” he says. “The feedback is collected for preventive maintenance and for feeding the production scheduling programs, because we need to schedule our vehicle orders so we can produce at high capacity with minimum cost plus high efficiency. These information systems and software infrastructure enable that.”
”There are more than 1,200 robots throughout the plants, with automation being utilised for almost 90% of operations in the paint shop”
There are a number of closed loop systems too, which Hosver says are used for traceability and monitoring data, in case of failures or if they need to go back and check at the point of fitment. For now it is all about feeding back into the capacity and maintenance process structures, but ultimately he says it is about moving towards a level of artificial intelligence.
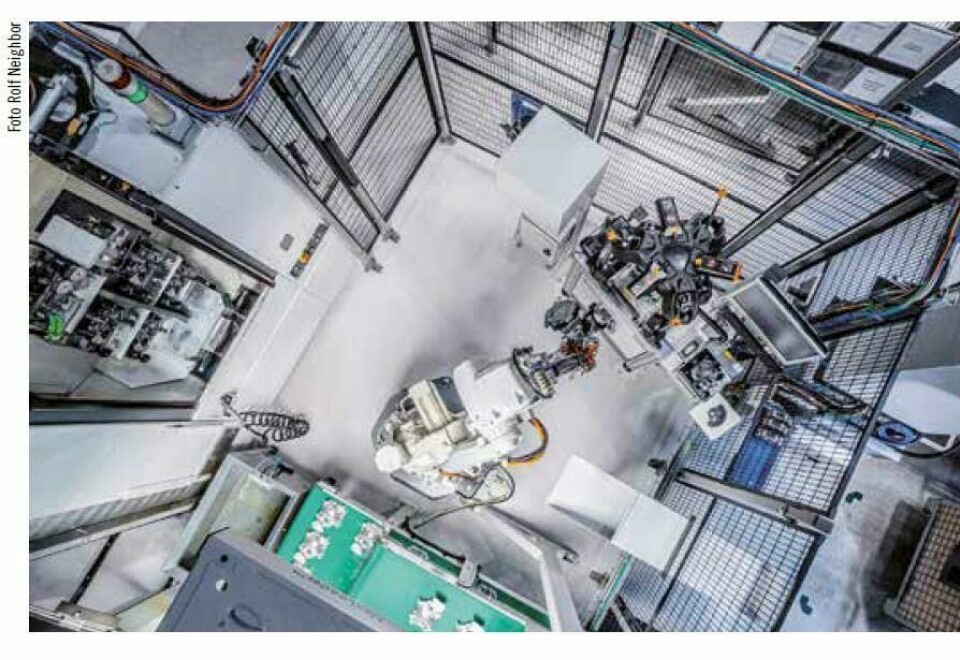
Peak automation from operations though material flow
There are more than 1,200 robots throughout the plants, with automation being utilised for 89% of operations in the paint shop. This includes the exterior paint surface quality automatic inspection system, automatic analysing and automatic dosing and a fully automatic sealer line.
In the body shop the automation number rises to 98% of processes, but that figure does not take into account the employees working on the lines.
”It’s all about creating automation using the best of hardware and software, but also the best use of people”
Güven Özyurt, Plant Leader, Ford Otosan
“We have two ways of calculating automation,” he says. “Process automation is 98%. If we include the racking, people loading parts into the stations rather than doing any process, that is 82%. We do have a level of automated racking through Automated Guidance Vehicles (AGVs) and robots, but we have some stations that we are loading by operators as well so that makes the overall automation level in the body shop, 82%.“
The plant of the future: Yeniköy
Yeniköy is described as the “plant of the future” by Hosver and his team and relies heavily on its fleet of AGVs which are essential to material flow. They have been designed in-house by Ford Otosan’s research and development centre in Istanbul and are tailor-made for the requirements of each plant.
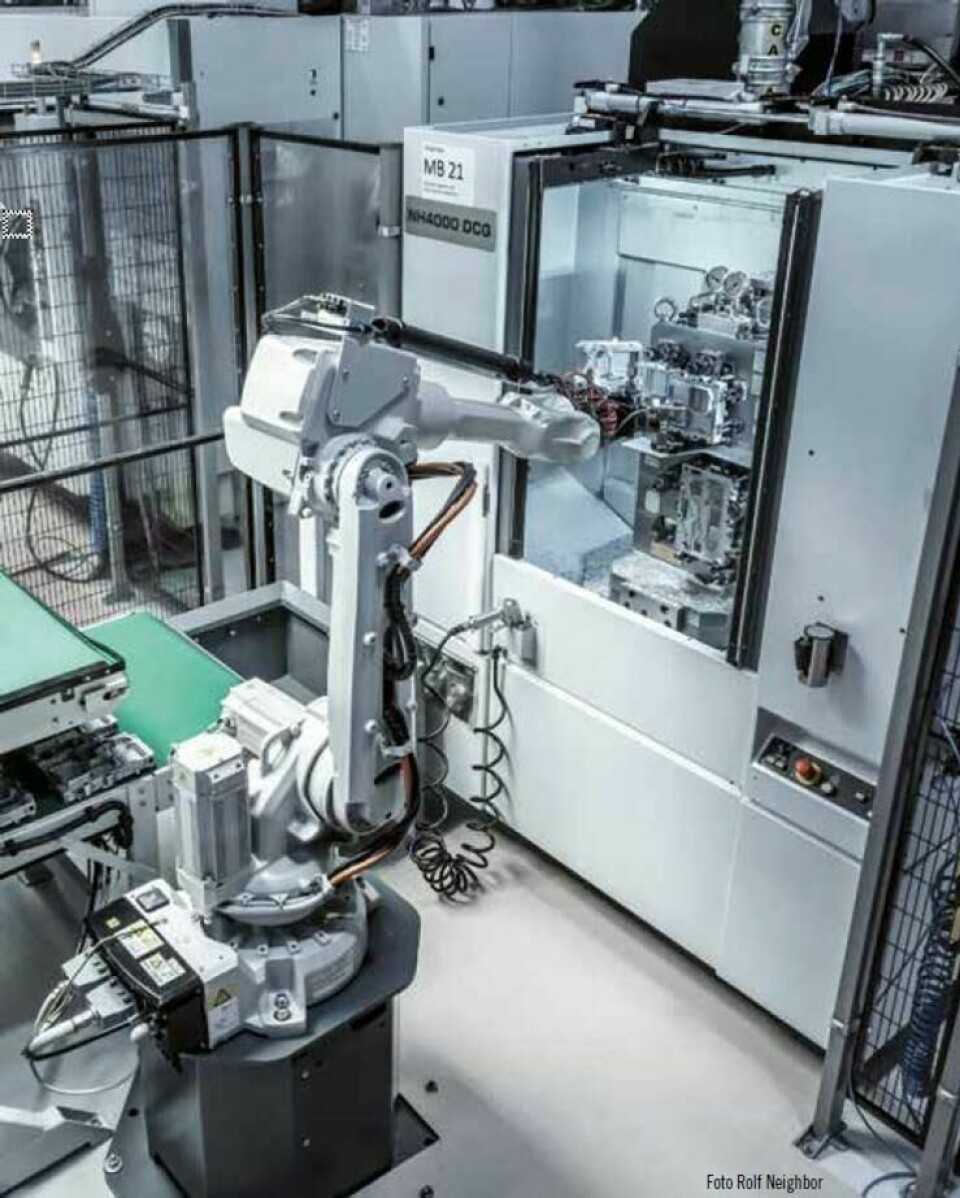
The AGVs are able to deliver components to individual stations on any of the lines and can deck engines or batteries. Some AGVs can also install loads directly into vehicles.
Every component is tracked using QR traceability and most are transported around the plant using AGVs and various other automated handling systems. These include elevators and overhead conveyors that can transport the bumpers, seats, wheels and tyres. They also carry the instrument panels (IP) to the correct stations. When it comes to the IP though, Hosver says automation can deliver it to the line and even load it, but the employees on the line tighten everything to make sure it is firmly in place.
Where employees really can’t go, is the impressive second floor of the double-decker body shop production line. It’s the first of its kind and operates on a ‘lights-out’ basis says Hosver. Robots don’t need lights. That’s also why the line can have restricted headroom, because robots won’t accidentally bump their heads. People do go in, but only maintenance staff.
“The plant target is to maximise the uptime and in order to maximise the uptime you need to establish the infrastructure of the connectivity”
Aysan Hosver, Plant Leader at Ford Otosan, Kocaeli Plant
“Where an area is fully automated we do not allow operators to get inside protected cells, because that is where robots are working,” he says. “Any employee working inside will lock the system and without that lock being removed by the operator, the system will not work.”
There are of course areas where people and machines do work together, but again Hosver says there are protective properties and processes in place to to ensure it is a safe working environment.
The end-of-line tests and quality checks are also mostly automated. Vehicles are loaded into their testing positions and the tests are run. The software contains all the algorithms required to check the properties and specifications that need to be verified.
It is all about creating automation using the best of hardware and software, but also the best use of people says, Güven Özyurt, Leader of Ford Otosan.
“The plant target is to maximise the uptime and in order to maximise the uptime you need to establish the infrastructure of the connectivity,” he says. “You should be able to allow machines to talk to each other and create data that is stored instantly so that you can create algorithms. These can be used to avoid breakdowns and quality issues and provide more information to the operational teams so they can excel further in the plant operations.”
”Ford Otosan now has one of the most advanced production facilities in the world, producing the highest number of derivatives with the widest range of powertrains”
Kocaeli among BMW and Renault plant cadre recognised by WEF for 4IR technologies
It would appear those operations are going well, because the investment in upgrading the levels of automation and digitalisation in the plant has been recognised by the World Economic Forum (WEF). The international organisation made the plant at Kocaeli part of its Global Lighthouse Network. The plant joins those from BMW and Renault that the WEF says have shown leadership in applying Fourth Industrial Revolution (4IR) technologies to drive change forward.
The Kocaeli plants will definitely keep driving forward. Among other projects, there are plans to reach the point of having a silent factory with wireless and rechargeable drills instead of pneumatic powered equipment. In 2025 it is expected that the 255,000 square metre Yeniköy facility will be producing 405,000 Ford and Volkswagen vehicles. It will have 6,600 employees working multiple shifts and sharing the responsibility of producing those vehicles with an automated system that is constantly learning.
Ford Otosan now has one of the most advanced production facilities in the world, producing the highest number of derivatives with the widest range of powertrains. It all seems rather appropriate for a business that is producing commercial vehicles with the widest range of uses and which are often viewed as the powerhouses of economic activity.