Scaling agility in auto manufacturing: Volkswagen and Toyota on flexibility, digitalisation, and workforce innovation
Through a series of insights shared by Chris Glover, executive vice-president of Volkswagen Group of America, Chattanooga Plant, and Jaime Moore, senior principal engineer at Toyota North America, the discussion called for a vital need for flexibility, collaboration, and technological innovation in navigating constant change.
As the automotive industry continues to navigate constant change, the ability to adapt quickly and efficiently is becoming a competitive differentiator. By embracing flexibility, leveraging digital tools, and fostering collaboration, manufacturers can not only meet current challenges but also position themselves for long-term success. At the AMS Evolution North America event in Detroit, Christopher Glover, vice president of production at Volkswagen’s Chattanooga Plant, and Jamie Moore, senior principal engineer at Toyota Motor North America, shared valuable insights into how agility is reshaping manufacturing strategies to meet the demands of a dynamic future.
The challenge of constant change
The pace of change in the automotive industry has reached unprecedented levels. The shift to electric vehicles (EVs), coupled with a growing focus on sustainability, has disrupted traditional manufacturing models. “The only constant in our industry right now is change,” remarked Glover, emphasising the multifaceted pressures facing manufacturers today. From navigating new regulations to addressing supply chain vulnerabilities, the industry’s ability to adapt quickly and become flexible has become a core competitive advantage.
Volkswagen’s Chattanooga plant exemplifies this adaptability. By integrating EV and internal combustion engine (ICE) vehicle production on the same line, the facility has hedged its bets against uncertain market dynamics. “One of the best decisions we made early on in Chattanooga was to integrate the production of electric and internal combustion engine vehicles on the same production line,” Glover noted. This approach includes creating adaptable infrastructure in areas like the body shop, where pre-installed flexibility capabilities allow for seamless integration of new product derivatives over time.
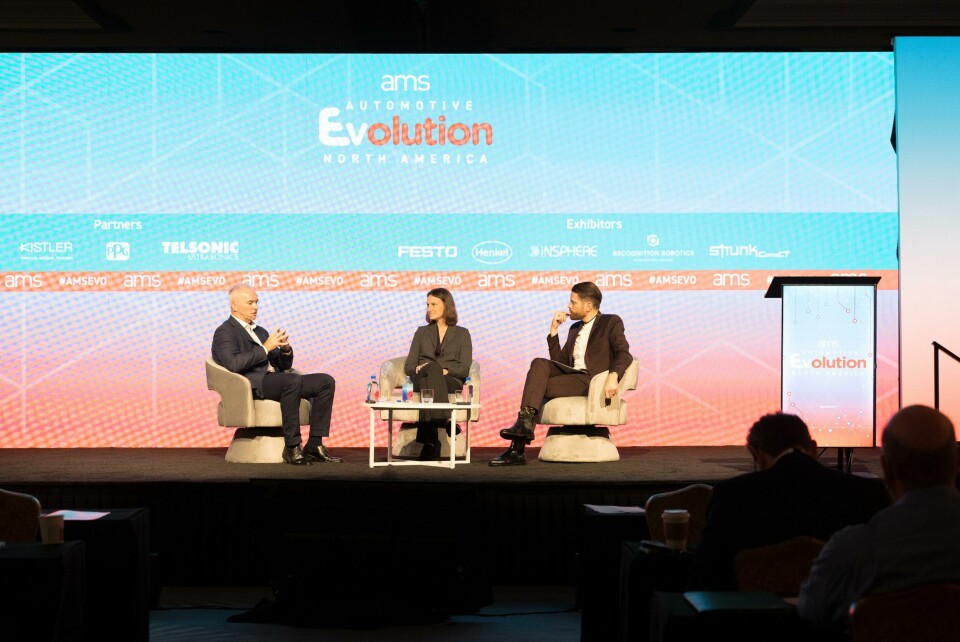
For Toyota, the challenge of constant change has reshaped the role of engineers. “Engineers now have to adopt a flexible mindset,” said Moore, highlighting how traditional silos are breaking down. Reflecting on the shift, Moore noted that engineers are no longer confined to their traditional roles; they must now juggle design, manufacturing and logistics considerations. “We need to build up a bigger skill set to meet the growing scope of needs. Engineers must now consider not only the feasibility of designs but also their manufacturability, logistical requirements, and lifecycle impacts.”
Flexibility in manufacturing processes
Flexibility is no longer a luxury—it’s a business imperative. Modern manufacturing facilities must be designed to adapt to evolving demands, whether from new product launches, regulatory changes, or supply chain disruptions. Both Glover and Moore stressed that flexibility needs to be embedded into every stage of the manufacturing process, from design to assembly.
Volkswagen’s Chattanooga plant offers a prime example of this principle. Glover explained how their body shops, one of the most capital-intensive areas of manufacturing, are designed with built-in flexibility to accommodate successive product derivatives. “Changing a body shop is the most capital-intensive adjustment, but by pre-planning for flexibility, we reduce pain points when adapting to new models,” he said. This approach minimises costly redesigns and ensures long-term value from initial investments. Similarly, their paint shops, though less complex, are equipped with advanced automation systems to handle diverse product lines efficiently.
At Toyota, the focus is on integrating flexibility directly into the design process. Moore shared how engineers are increasingly considering manufacturability and logistics early on, ensuring that designs are both feasible and adaptable. “With limited time, you don’t have time to make mistakes,” she emphasised, highlighting the importance of getting designs right the first time. This proactive approach reduces lead times and enhances collaboration between design and manufacturing teams.
“We’re constantly adding new requirements—regulations, customer preferences, manufacturing needs—but we’re not removing any of the old ones. The result is an increasingly complex design process,” she said. This makes simplification a strategic priority. Moore explained how Toyota has moved away from short-term cost-saving measures, like reducing part sizes, if they increase complexity in the long term. “If it doesn’t add value to the customer, we’re not doing it,” she added.
The role of digital tools in scaling agility
Both speakers highlighted the transformative potential of digital tools in achieving manufacturing agility. Digital twins, AI, and data-driven decision-making are becoming integral to the manufacturing landscape. Glover noted: “We’re working with vast amounts of data, and the challenge lies in how to handle and manipulate it effectively.” He emphasised that AI can democratise access to data processing, empowering engineers and decision-makers alike.
Volkswagen has been at the forefront of leveraging digitalisation. Glover explained how data management systems are being used to identify and address production issues in real time. “We have access to unbelievable amounts of data. The challenge is how to handle it and use it to run the business effectively,” he said. AI-powered systems are democratising data analysis, allowing employees across functions to generate actionable insights. For instance, AI-driven vision systems are used to detect defects closer to their source, reducing costly rework at later stages of production.
At Toyota, digital twins are being employed to simulate manufacturing processes, allowing teams to identify potential bottlenecks and inefficiencies before they arise. “We can’t build prototypes for everything anymore,” Moore noted. “Digital tools allow us to iterate faster and collaborate more effectively.” These simulations also foster better communication between design, manufacturing, and supply chain teams by providing a shared visual framework for problem-solving.
However, Moore cautioned that digital tools must complement—not replace—human collaboration. “Simulation can’t replace the value of face-to-face conversations around a prototype,” she said.
Collaboration across departments and supply chain
The complexities of modern manufacturing and supply chain requires collaboration and constant communication across departments from design to tier suppliers. “We’re an ecosystem,” Moore stated, emphasising the interconnected nature of automotive manufacturing. She advocated for involving suppliers and other stakeholders early in the design process to ensure seamless integration and efficiency. This early collaboration reduces lead times and improves the final product’s quality.
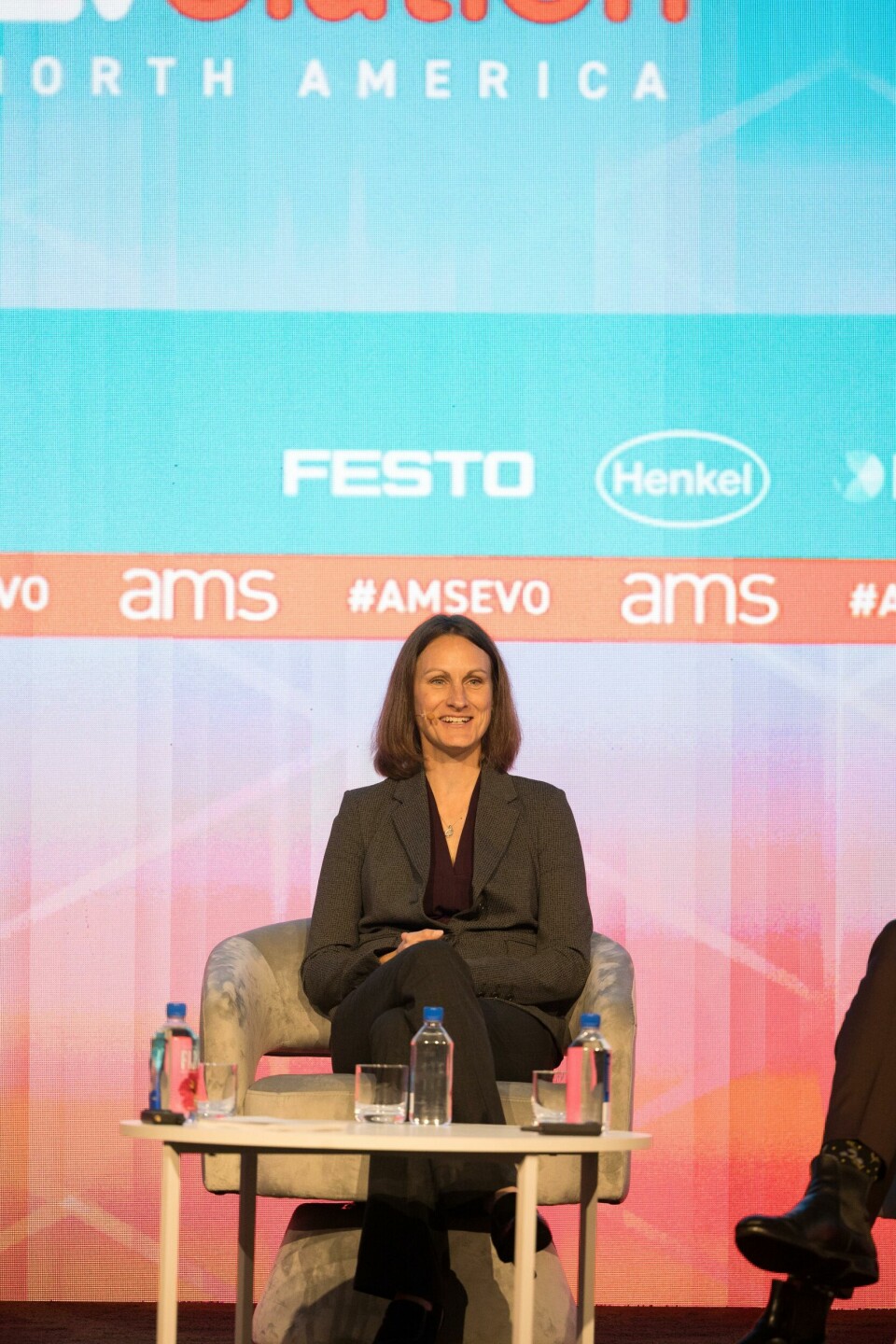
Glover highlighted the importance of supply chain visibility, particularly in an era of just-in-time (JIT) manufacturing. Glover emphasised the need for better visibility into Tier 2 and Tier 3 suppliers to mitigate risks from geopolitical and logistical disruptions. “If we can get to grips with what’s happening in the supply chain, it helps us modify production schedules proactively,” he explained. Volkswagen is exploring ways to use digital tools to gain deeper insights into their supply chain, enabling them to anticipate disruptions and adjust production schedules accordingly.
Both Glover and Moore discussed the need for cross-functional training to foster a culture of collaboration within their organisations. This approach not only enhances operational flexibility but also prepares employees to navigate the complexities of modern manufacturing.
Workforce development and retention
A skilled and adaptable workforce is the foundation of manufacturing agility. However, retaining and developing talent has become increasingly challenging in a competitive labour market. Both Toyota and Volkswagen have implemented innovative strategies to address these challenges.
At Volkswagen, Glover tackled labour retention head-on, reducing attrition at the Chattanooga plant from 35% to 10% within two years. “Labour retention creates stability in your process,” he explained. “It’s a great enabler of flexibility because you retain knowledge and skills.” Strategies included offering competitive benefits, providing opportunities for professional growth, and fostering a positive workplace culture.
Moore emphasised the evolving skill set required for engineers in today’s environment. “We need to build up a bigger skill set to meet the growing scope of needs,” she said. Toyota has implemented rotational programmes to expose employees to different areas of the organisation, enhancing collaboration and creating a more versatile workforce. This approach aligns with industry trends; according to the World Economic Forum, 54% of employees in manufacturing will need significant reskilling by 2025 to keep pace with technological advancements.
Balancing complexity and simplification
As automotive manufacturers scale up their operations, the interplay between complexity and simplification becomes critical. Additionally, with the growth in customer and product demands, manufacturers must navigate the tension between offering diverse options and maintaining streamlined operations.
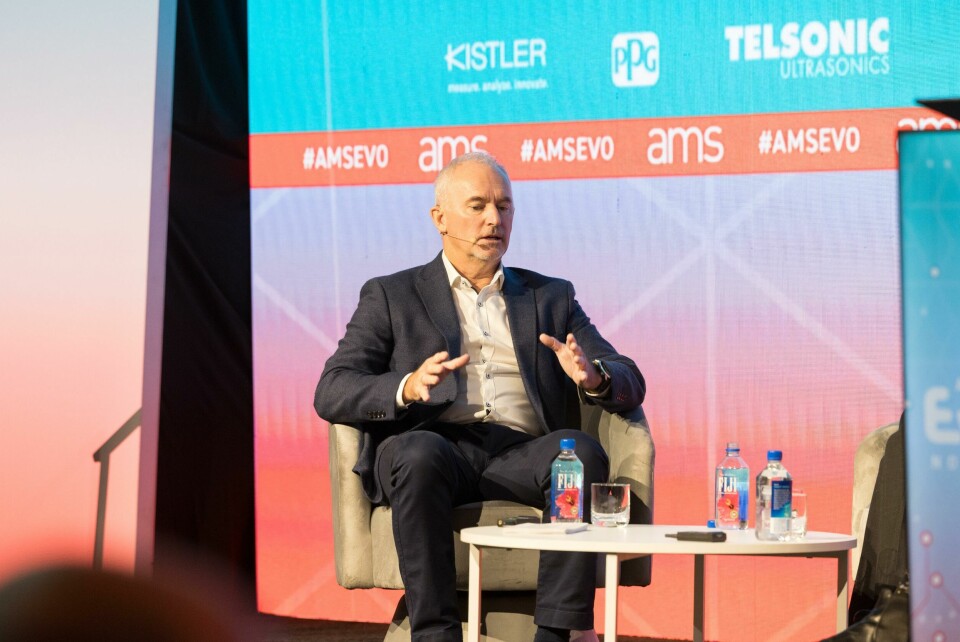
Glover acknowledged this challenge, noting that automation and advanced systems can handle complexity but at a cost. “The key to flexibility comes down to training and manpower development,” he said. By investing in workforce skills, Volkswagen has been able to manage the complexities of producing diverse vehicle architectures on a single assembly line. He also outlined how automation and advanced systems play a pivotal role in managing this balance, but labour retention also emerges as a key factor.
Moore highlighted how Toyota is addressing this trade-off in the design phase. “If a design change doesn’t add value to the customer, it’s often not worth the added complexity,” she explained. Engineers are increasingly focused on simplifying designs to reduce logistical and manufacturing challenges, ensuring that complexity is introduced only where it delivers tangible benefits.
The insights shared at AMS Automotive Evolution North America 2024 provide a roadmap for navigating the future of automotive manufacturing. From integrating digital tools to fostering cross-functional collaboration, the strategies discussed reflect a broader industry shift toward resilience and adaptability.
Reflecting on the broader implications, Glover concluded, “Flexibility is a competitive edge, but it’s also a mindset. It requires constant learning, adaptation, and a willingness to embrace change.” For Moore, the path forward lies in balancing fundamentals with innovation. “You can’t win if you can’t block and tackle, but you also need to be ready to throw the ball down the field,” she said, referencing Toyota’s emphasis on foundational skills as a springboard for innovation.
“You have to embrace change and be willing to innovate. If you’re not, you’re falling behind,” Moore added. By prioritising agility, manufacturers can not only navigate the complexities of today but also position themselves for success in the future.
At the event, Jamie Moore spoke to our chief content officer, Christopher Ludwig, separately on the evolving role of engineers in manufacturing. Check out the full interview below: