Hot off the printer
More automotive companies are discovering the benefits of additive manufacturing for rapid prototyping
In April, the first race of the 2015 World Endurance Championship at the Silverstone racetrack in the UK will see the debut of the Strakka DOME S103, a low-slung coupe designed and developed by two organisations on different sides of the world. One is Japanese automotive design consultancy DOME, the other is UK race team Strakka Racing, which is based close to the circuit where the car will make its first competitive appearance.
As team principal Dan Walmsley explains, the car will be the first in which Strakka has had a major design input; previous vehicles driven by the team, which has been racing since 2007, were bought in and at most “tweaked” to enhance their performance. Walmsley says the vehicle was initially developed under an “aggressive” plan that was intended to see it start racing in 2014, but in April of that year Strakka decided it was dissatisfied with the progress and decided to take over further development.
For an organisation with just 42 employees and no previous experience of intensive vehicle development, Walmsley admits it was a bold step. One of the ways the company set about preparing for the task was to equip itself with an in-house additive manufacturing capability, courtesy of a Stratasys uPrint SE Plus 3D Printer. Strakka installed the machine in the summer of 2014 after preliminary discussions with Stratasys suggested that the technology could help to compress development timescales.
The machine was initially used for the conventional additive application of rapid prototyping to test the form and fit of parts most likely to be manufactured for actual use from carbon fibre materials. The parts were relatively simple, for example brackets and aerodynamic covers. In fact, the machine was not merely used for prototyping but also led to an increase in the number of additively manufactured parts on the car.
This experience caused Strakka to reassess its previous perception of such parts. “We realised that they were a lot stronger and more versatile than they used to be, and that opened our eyes to other things we could do,” states Walmsley. Within a few months, Strakka was fabricating the dashboard for the vehicle – a structure that had to be both lightweight and strong even though it also contained attachment points for switches and apertures for the display screens of rear-facing cameras.
“We made the first one as a mock-up but found that its material properties exceeded our expectations,” he confirms. According to Walmsley, the most likely alternative material for the dashboard would have been some form of carbon composite. A major disadvantage of that approach, though, would have been the much greater cost – for tooling more than materials.
Rapid design iteration is another benefit Strakka has gained. Walmsley gives the example of the ducts that allow air to reach the brakes for cooling purposes, saying that during track testing the team was able to achieve “a nearly 24-hour turnaround period” for making modified units and fitting them to the vehicle. “We have simply never been able to achieve anything like that before,” he states. The same is true for wind-tunnel testing. Walmsley says that the ability the company now possesses to produce new parts extremely rapidly means that ideas can be tried out in less time than before: “We can do in seven weeks what might previously have taken 20, and that is a game-changer".
The precision of the parts produced by the additive method is also a step beyond what was previously possible. “CAD and car are now the same”, as Walmsley puts it.
Mastering additive manufacturing
The in-house machine is not the only additive manufacturing resource that Strakka has exploited. Given that it has a working envelope of roughly 14 cubic inches, some larger components – including the dashboard – have been made using bureau services in the US, facilitated by Stratasys. Strakka has also benefited from the advice and support of additive manufacturing company Laserlines, in Banbury, UK. Nevertheless, Walmsley is adamant that Strakka has now become an autonomous user of the technology: “If we want to make something, we just fire the machine up. We may not be experts, but we are self-sufficient.”
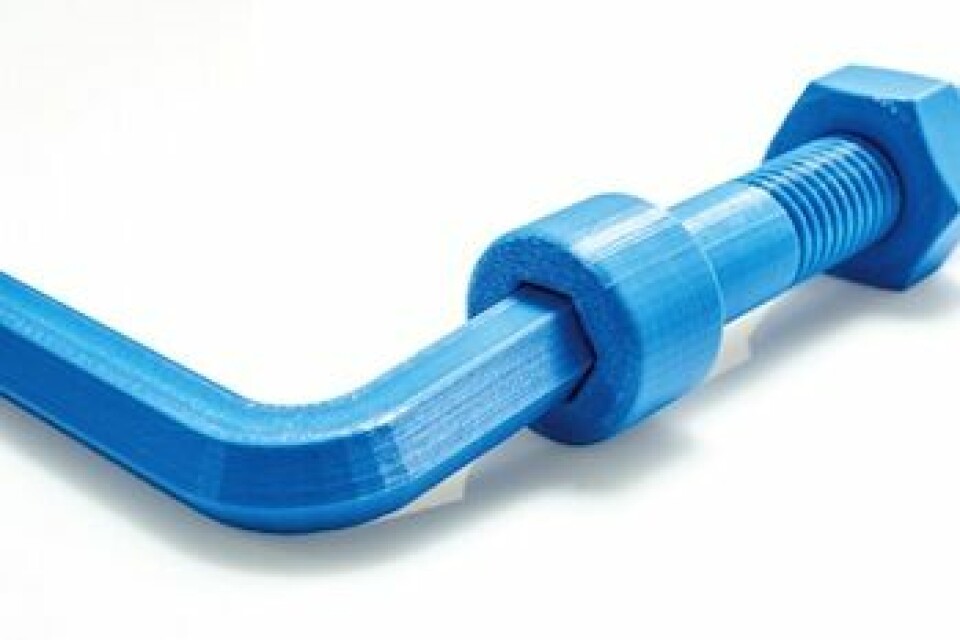
Though the strength of the additive parts has been a surprise, Walmsley confirms that they are not being used in applications where safety-related impact resistance is a requirement. The list so far includes: the brake duct, engine air intake, dive planes, brackets, dashboard and front-nose cover plates.
The really crucial factor for Strakka is saving weight. Walmsley says that the comparative figures are straightforward: a part weighing 1kg in steel would be around 300g in aluminium and 150-250g in additive polymer. A carbon fibre counterpart might be as little as 100g, but entails a time and cost trade-off.
The car has not been raced yet but it has completed 3,500km of test-track runs, during which all the additive parts have performed to specification. “None of them have failed,” Walmsley confirms. The technology has established itself as a core competence for Strakka that is essential to what is now a fundamental objective: “To transition from being a race car operator to a race car manufacturer”.
Making small components
Another company that has also just made its first foray into in-house additive manufacturing – to make perhaps less exciting but rather more pervasive products – is components maker TR Fastenings. Managing director for European operations Geoff Budd confirms that halfway through 2014 the company installed a MakerBot Replicator machine at its site in Uckfield, UK. Budd says the move was prompted by a previous contract win from an automotive seating manufacturer for a “particularly complex” part. Prototyping using conventional machining techniques cost “hundreds of pounds”, says Budd, but within a year the customer had decided that the part no longer met its requirements.
So, TR decided to make an investment of “less than £5,000” for a machine that now provides it with the ability to make what are relatively inexpensive polymer representations of parts that will eventually be made in metal.
In addition, TR has acquired the licences to produce the Strux self-clinching and Matherd cross-threading prevention systems, both of which involve producing small components in which a basic design is customised to a particular application requirement. TR expects that producing part models with the MakerBot should prove more than useful in securing orders. The machine is able to make parts with elements such as screw threads that can move relative to each other, so it facilitates much more than just product visualisation and manual form-and-feel validation. “It can show both what the part will look like and how it will function in use,” Budd confirms.
Budd says the machine has already been put to work making parts that have been shown to prospective customers that he describes as “tier one suppliers” to the automotive industry. Sales staff have apparently found it very effective and prospective customers have reacted in a “positive” manner to being able to view and handle models of parts that may be only a few centimetres in length.
But Budd is also candid enough to admit that TR has perhaps come “a bit late” to its use of the technology. The company is now thinking of taking the bolder step of adopting additive laser sintering techniques for making metal parts, though no definite decision as yet been made.
A new technology gets off the Mark
But what about developments in additive manufacturing technology itself? Within the last year, a newcomer has arrived on the scene with a technology that it claims could be groundbreaking in the automotive and other industries. It is the type of claim that is often made, but which in this case might actually be true.
The company is MarkForged of Waltham, Massachusetts. What it has brought to the market is a machine called ‘the Mark One’, which it describes as the first-ever additive manufacturing machine that can make genuine composite materials with continuous reinforcement fibres running through them. Jeff Klein, creative director for MarkForged, explains that the machine has two print heads and that this combination is what provides its unique capability.
One is a fairly conventional additive ‘fused filament fabrication’ extrusion device of the type used for fused deposition modelling, which can create layers of either a robust nylon material or a low-cost polymer alternative called PLA. He adds that the nylon is a special formulation devised by MarkForged that ensures good adhesion between the different layers even when reinforcement fibres are present. The nylon layers can be made with a resolution of 100 microns. Meanwhile, the polymer can make simple models with no need for any reinforcement to test form and fit.
The other is MarkForged’s own patented device of a type it terms ‘continuous filament fabrication’ that can extrude continuous lengths of reinforcement fibre in carbon fibre, Kevlar or fibreglass. The fibres are composed of multiple thin strands pre-impregnated with a thermoplastic material, again specially formulated, which helps the fibres to bond both with each other and with the nylon additive material. Klein says the materials involved are similar to those used in conventional composite parts manufacture, but the fundamental difference is that there is no need for procedures such vacuum bagging and baking in an autoclave.
The Mark One is a very lean desktop machine that can make parts up to 320x132x160mm in size. Klein says that by weight, these parts are “10-15% stronger than if they were made from 6061 aluminium.” Larger fabrications can be produced by joining smaller parts with a straightforward mechanical fixing method. Another highly innovative feature of the machine is that operations can be paused to allow the insertion into an additive fabrication of a completely independent part such as a bearing, which can then be securely embedded in the completed part.
The future of additive for automotive
Klein is understandably enthusiastic about the prospects for the technology across multiple industries, especially automotive. One likely benefit derives from the ability of the machine to use fibreglass as a reinforcement material. Apart from reduced cost in applications that do not require the strength that carbon fibre might supply, Klein observes that fibreglass is transparent to electromagnetic radiation, and for the most part also to radio waves. This offers the prospect of being able to fabricate strong lightweight housings from fibreglass reinforced nylon for electronic units that may be required to communicate wirelessly with other systems, either in the car or – as is increasingly the case – external to it. Whereas a metal housing might impair the operation of the electronics, such a composite material could be ideal, Klein notes.
The potential benefits do not stop there. An additional advantage is that the reinforcement material can easily be used selectively within a single part so that only those regions that need extra strength will be reinforced – an obvious attraction when the reinforcement material is something as expensive as carbon fibre. Furthermore, since nylon is a non-abrasive material, another possible application might be in the manufacture of jigs and fixtures used to hold metal parts during assembly operations. “Nylon won’t scratch metal,” observes Klein.
So far, only one automotive company has made use of the MarkForged technology: local specialist Aeromotions, which makes aerofoil wings for attachment to cars used for track racing. There is a significant degree of shared ownership between MarkForged and Aeromotion, Klein explains, though the two operate independently.
The Aeromotions wings are made of carbon fibre, while the struts that hold them above the car body are aluminium. Each element is made in batches of as many as a hundred, though there are two different wing types and they have been fitted to as many as 25 vehicle models. But the mounting units, or wingbase, which accommodates the struts and is then attached to the car, must be customised to the shape of the particular vehicle. Klein says that, once a configuration is finalised, the volumes involved will make conventional machining the most likely production method, but that prototype units made by the MarkForged technique have been used to test “form, fit and function”.
The prototype units are of a ‘sandwich’ construction. The nylon honeycomb core divides outer layers in which carbon fibre reinforcement provides the required strength. The company says that two such units have been used to hold in place an aerofoil wing capable of generating 860lbs of downforce at 200mph. Moreover, adds Klein, the MarkForged technology has produced fixtures that hold the wings while the holes for attaching the aluminium struts are drilled into them – an application that illustrates the non-abrasive surface finish of the parts.
It seems that a technology has now emerged which will enable additive techniques to be used to manufacture parts for applications demanding much greater physical resilience than has previously been possible. How it may be exploited in the global automotive industry remains to be seen.
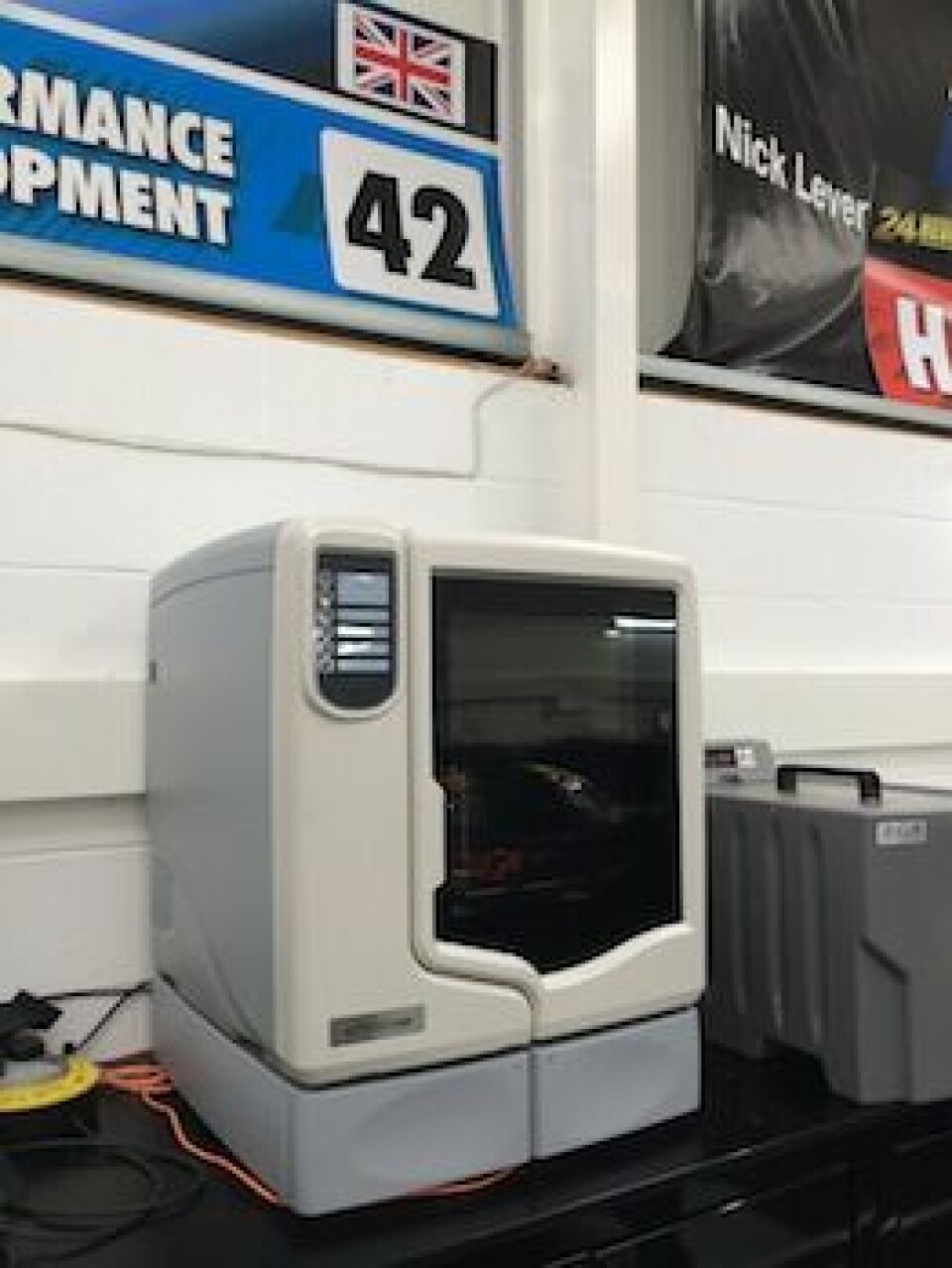
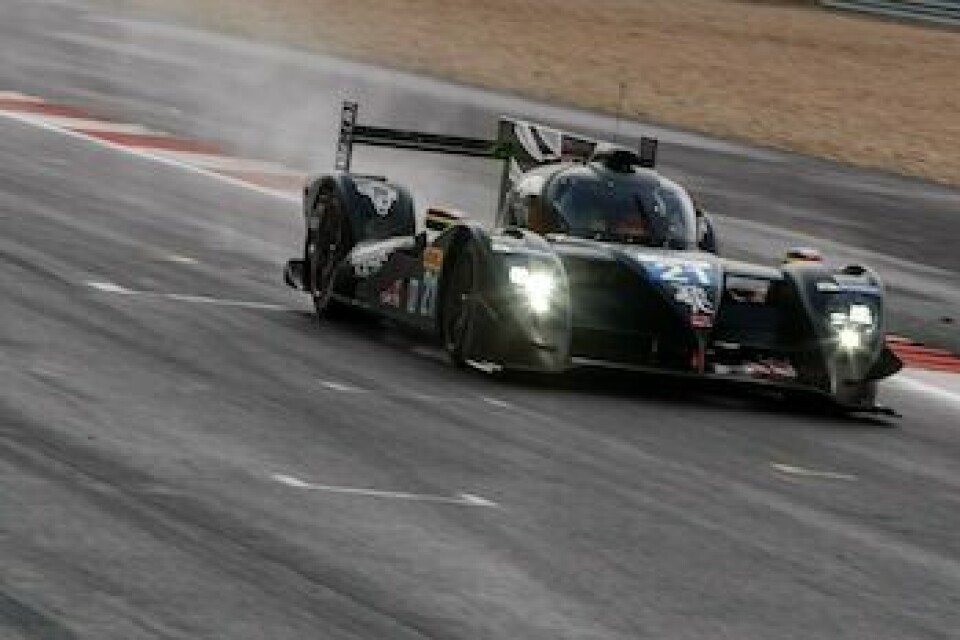