Bloodhound’s additive challenge
Advances in additive manufacturing are being put to the most stringent of tests as the Bloodhound Land Speed Record project makes its first high-speed runs. Chris Pickering speaks to the engineers behind the project and the contribution made by 3D-printed components, one of the key production technologies helping to make the attempt possible
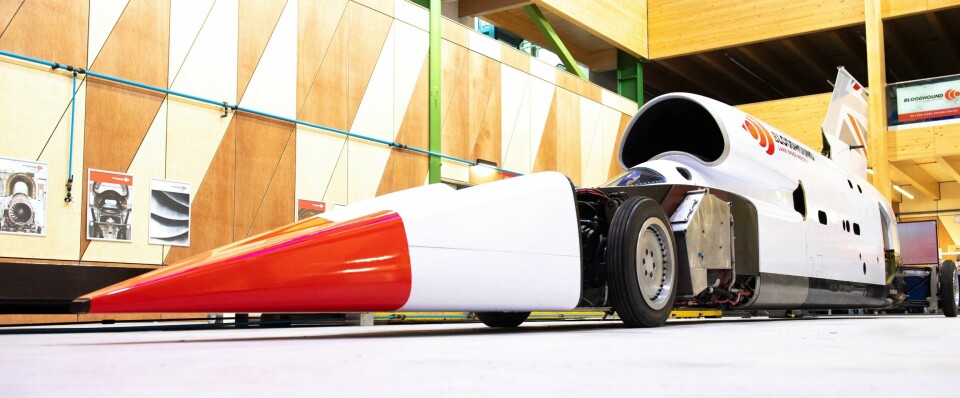
Bloodhound is go! After years of development, a complex manufacturing programme and a series of financial hurdles, this 135,000 horsepower supersonic car has begun its high speed testing and already ranks as one of the fastest machines ever to travel on land. And as it spears across the desert surface of the Hakskeen Pan in South Africa, the very first thing that comes into contact with the air stream is a piece of 3D printed titanium at the tip of Bloodhound’s nose. That’s just one of dozens of areas where additive manufacturing has played a key role in getting the car ready for its mission to break the World Land Speed Record.
The numbers involved are staggering. For the desert runs, Bloodhound is using wheels machined from solid aluminium – each weighing 91 kg. For the first batch of test runs the team is working its way up through the subsonic region in 50 mph (80 kph) increments, carefully analysing the data at each stage.
The plan is then to return to South Africa – potentially in late 2020 – for an attempt to break current record set by Thrust SSC at 763 mph (1,228 kph). Just how fast Bloodhound might go remains to be seen, but the original calculations for the project assumed a theoretical top speed of 1,000 mph (1,609 kph). By that point, those giant aluminium wheels would be spinning at 10,200 rpm and their outer rims would be subject to some 50,000 radial G.
This is the extreme world in which Bloodhound’s additive components will also have to survive. At that speed, the car would be subject to more than 20,000 kg of skin drag. The pressure on the 3D printed nose tip alone could be as much as 12,000 kg/m². It’s a dramatic demonstration of just how far additive manufacturing has come in recent years.
Producing the nose tip to the current design would have been extremely challenging with conventional methods. Inside the hollow part there’s a complex honeycomb structure to maximise its strength-to-weight ratio, while the outwardly flat sides are, in fact, subtly curved for aerodynamic reasons. Machining it from solid titanium would have resulted in as much as 95 per cent of the expensive raw material going to waste – and that’s assuming you could have got tool access to make it possible.
Instead, the Bloodhound engineers turned to a metal powder bed fusion technology developed by Renishaw. Here, a thin layer of fine metal powder (in this case Ti-6Al-4V titanium alloy) is deposited across the build plate, before selected areas of the powder are melted by a laser. The process is then repeated to build the part up layer-by-layer. This is just one of a number of additive manufacturing processes that have been employed to create functional parts for Bloodhound in carbon, titanium, and steel.
“Since the beginning of the project we’ve seen the emergence of a lot more engineering-grade additive materials,” explains the team’s lead mechanical and composites engineer, George Morris. “They’re much easier to analyse these days too – we can run an additive part through a finite element simulation and be confident of getting accurate results. Perhaps five years ago – and certainly 10 years ago – that wouldn’t have been the case.”
Elsewhere, Graphite AM’s Carbon-SLS material has been used extensively for ducts and bracketry. Morris points to a part that’s been dubbed the ‘trouser duct’ on account of its of broad waist and two ‘legs’ sticking off. This features compound curvature, strengthening ribs and integrated bracketry that would be complex to produce with conventional methods.
“If you look at the way that the bracketry has been blended into the duct, it just wouldn’t be cost-effective to do that as an integral part of the component with traditional techniques. Plus, we needed a one-off part that could be manufactured quickly,” comments Morris. “Very few parts on Bloodhound are ever going to be made in multiple batches, so it’s not cost-effective to produce moulds for composite structures. Additive manufacturing is ideal for those circumstances.”
Perfect grip
Another example of the use of additive manufacturing in Bloodhound is its titanium steering wheel. The original design concept was developed by an intern working on the project and rapid prototyped in Nylon by Belgian company Materialise. The Cambridge Design Partnership was brought in to refine the part, which was then manufactured by Renishaw.
“The steering wheel is a great example of something that would have been extremely difficult to produce with traditional machining. It’s a complex external shape – moulded to [Bloodhound driver] Andy Green’s hands – but it’s completely hollow,” explains Morris. “There’s a lot of detail on the inside of the part to accommodate all the electronics, which we were able to put in straight from the finite element model.”
Even with the use of additive manufacturing, this part presented some challenges. At the time, the size of the machines didn’t allow it to lie flat during production, so it was sintered at an angle with extensive use of support material. Initially, the Bloodhound team also encountered problems with cracking due to thermal lag as the successive layers cooled, but these issues were soon overcome.
The finished item is a beautiful piece of engineering. It’s arguably somewhat over-engineered for the requirements of a steering wheel – Formula 1 teams achieve similar functionality with traditional composite designs – but this project has always been about promoting new technology.
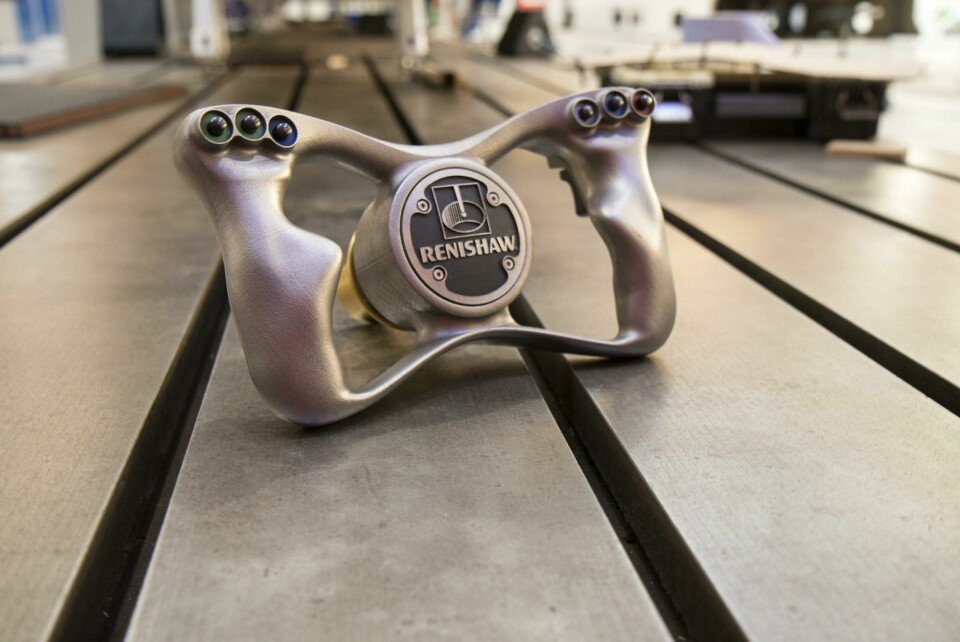
“Part of Bloodhound’s remit is to serve as an educational platform and a R&D exercise, so there were some areas where we decided to pursue a particular technique to demonstrate the technology,” comments Morris. “On the other hand, we’ve also been careful to go with materials and techniques that are backed up by plenty of empirical data to ensure safety.”
It’s been a learning process at times, he admits. Much like composite production, additive manufacturing has its own set of rules. First, it’s necessary to understand the properties of the materials and how to model them. With that comes the need to understand strengths and limitations of the manufacturing processes. Finally, there’s a design for manufacturability (DFM) aspect.
“It can be quite difficult for a traditionally-trained engineer to get their head around additive manufacturing,” comments Morris. “You need to think of it as an additive part from the outset. You also need to play to the strengths of the process and the geometry it allows. For example, the plastic materials tend to take a long time to dissipate the heat from the sintering process, so you want to maintain the wall thickness throughout the part to prevent it warping or cracking as it cools down. Similarly, with metal components, you can’t generally have an overhang at an angle of less than 45 degrees as the material has to be self-supporting. On the other hand, you have a lot more freedom in the geometry than you would with traditional methods.”
It’s a thought process that’s gradually becoming more ingrained in young engineers, he notes: “We’re now starting to get people through who used these techniques at school or university who are perhaps more comfortable with them than some of the more experienced engineers.”
Record breaking
The Bloodhound team had to work flat out to get everything ready for the first high speed runs in South Africa. Here again, the flexibility and short lead times of additive manufacturing proved to be a real bonus. “We don’t carry out any additive manufacturing on-site. Some of the components have had to be designed and manufactured in very swift order, so the collaborative relationship we have with our suppliers has been really important,” notes Morris.
Once they’ve digested the data from the first batch of high speed runs, the Bloodhound engineers will switch their attention to re-fitting the car for its record attempt. In some respects that will represent an even bigger challenge. Bloodhound has been designed around a twin-engined configuration, with a hybrid rocket slung underneath the jet engine, but the initial tests have been carried out on jet propulsion alone. While the basics are already in place to support the rocket installation, there will be a lot of detail engineering required to make it possible.
“One of the main changes that we’ve got planned is to remove the internal combustion engine that was originally designed to drive the fuel pump for the rocket motor and replace it with an electric motor driven by a battery,” explains Morris. “The internal cooling systems required for that battery will need to be packaged in a very tight space. That means the ability to manufacture pipes with complex geometries will be very important, so this is one area where we’re likely to use additive techniques.”
Once that transformation is complete, it’s hoped that Bloodhound will go faster than any other car has been before. In fact, given the scale and complexity of the project it’s a very real possibility that it could be faster than any car will ever go again. That truly would make it a landmark engineering achievement and one where additive manufacturing had played a major role.