Oxsilan expectations
Engineers from GM’s Orion plant in Michigan describe a successful conversion to a thin-film pretreatment from Chemetall
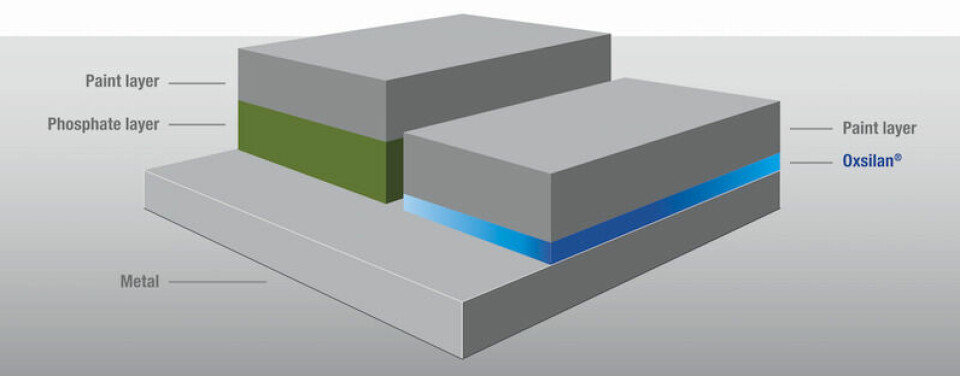
The Surface Treatment global business unit of the Coatings division of BASF, operating under the Chemetall brand, sets out the story of the highly successful conversion and launch to full production of Oxsilan thin-film pretreatment at the GM Orion Assembly plant in Lake Orion, Michigan. The Chevrolet Sonic and Chevrolet Bolt EV are manufactured there, representing 62,000 units per year for GM.
Daniel Green, GM Vehicle Systems Global Paint Materials and Facilities – Pretreatment and Electrocoat Engineer, shared the experience. “GM is continuously evaluating technologies as part of our passion for earning our customers for life. We already had a relationship with BASF and were ready to test both the synergy and co-existence of BASF and Chemetall, and the synergy and co-existence of Oxsilan thin-film pretreatment and CathoGuard 800 E-Coat, which was already in place.”
Green continues, “We converted in December of 2017, and ran ‘beta’ production for the first three months of 2018, watching very carefully. The quality improvements and increased cost efficiencies were striking – no streaking, mapping, or defects in the surface quality, no rinse additives needed, prolonged rinse life cycles saved water and energy, prolonged cleaning reduced stages and labour. Further, the initial conversion itself was timely and flawless, an incredibly smooth and successful process.
Chemetall experts, working closely with the Orion experts, really came together with care and attention to deliver a safe and effective changeover. It was simply a fantastic partnership. As of April, 2018 we are in full production with the Oxsilan thin-film pretreatment and we are very satisfied.”
Stacey Meador, Business Manager of the Chemetall’s North American Automotive Team, agrees: “GM, BASF, and Chemetall all share a deep commitment to innovation and sustainability. GM was now able, under the umbrella of approved partner, BASF, to evaluate the exceptional technological improvements that could be provided by our proprietary Oxsilan technology. BASF has a long and positive partnership with GM, having been awarded GM Supplier of the year 13 times in the last 16 years.”
Paul Krause, Chemetall OEM Key Account Manager, adds, “Oxsilan was designed for multi-metal surface treatment applications for OEMs, to noticeably improve corrosion protection and paint adhesion while offering significant reductions in water consumption, effluents, and energy. Oxsilan will work well with any modern E-Coat system.”
Chemetall, with a long history of innovation and dedicated to process improvement and sustainability, began developing a zinc phosphating alternative, a silane-based pretreatment which became Oxsilan, back in 2007. Chemetall identified two major trends in automotive OEM, that are now a crucial part of today’s manufacturing: lightweighting, and multi-metal compatibility, with a focus on aluminium substrates. In terms of quality performance, it is comparable to the zinc phosphating process, and in terms of its technical and economic feasibility, the new technology is clearly advanced.
What is Oxsilan?The base materials for the Oxsilan technology are zirconium and silanes. During the manufacturing process the silanes are hydrolysed and converted to polysiloxanes. During the coating process, the reactive silanol groups are chemically bonded to the metal surface as well as to the paint coating. Heat treatment, which follows the curing of a subsequent cathodic electro-painting (E-Coat) further cross-links the polysiloxanes creating a coating layer in the range of 100nm, thereby reducing materials consumption and pretreatment times, and increasing productivity: improvements of up to 65% have been realised in practical applications.
This thin layer is sufficient to achieve the same degree of corrosion protection as a zinc-phosphate coating which is ten times thicker. This has been proven in combination with many paint systems. The numerous functional groups present in the polysiloxanes contribute to the excellent paint adhesion. Additionally, Oxsilan offers considerable potential for process optimisation. With the Oxsilan technology, Chemetall has developed a sustainable, efficient, and economic pretreatment portfolio that exceeds today’s customer demands and industry trends in a variety of ways (see top image).
Oxsilan is the today’s thin-film technology of choice and meets GM’s pretreatment requirements. Chemetall was the first company to introduce a multi-metal thin-film technology on the market — long before most of the current developments had taken place. Now, Oxsilan represents a proven alternative — comparable in terms of quality to zinc-phosphating or chromating processes.
Almost 10 million cars on the road today have been treated with Oxsilan since May of 2009. Oxsilan is a proven technology, with global performance in more than 400 lines. This thin-film technology clearly shows advancements in terms of higher productivity and multi-metal capability, resulting in considerably lower process costs.
Oxsilan facilitates multi-material constructionThe performance requirements for vehicles and components are constantly expanding: more functionality, higher speed, stylish design, and increased safety are all demanded. To meet those expectations at a technical, cost-effective, and environmental level, new substrates are needed. However, single materials alone are not the answer to this ever-increasing list of demands. The solution lies in combining materials. Hence, multi-material design is becoming more important and with it, the need for a corrosion protection functionality with multi-metal capability. All common metals can be treated with Oxsilan. The increasing mix of metal substrates is a challenge conquered by Oxsilan. Traditional pretreatment technologies are not flexible enough and the set-up times are often too long to treat the substrate-mix. The Oxsilan technology is by its very nature a multi-metal process. All common metals and alloys in any combination can be treated with this thin-film technology.
The approach of the Oxsilan thin-film technology is quite unique. Chemical reactions take place with both the metal surface and the paint layer, forming strong bonds. Depending on the specific functional groups in the diverse Oxsilan systems, the pretreatment process can be adapted to different substrates and paint systems. The extremely low etching rate means embrittlement cannot occur and thus the pretreated components can withstand higher loads when in service. At Chemetall, we are dedicated, so you can expect more.
OXSILAN SUPPLY
Easy changeover from conventional processes to Oxsilan: Manufacturers seeking a paint and pretreatment system upgrade should consider taking a step towards the future. Many years’ industrialised experience has shown that existing processes can be converted effectively, with limited investment.
Eco-friendly production techniques are directly linked to cost savings: Major advantages of changing over to the Oxsilan technology are its environmental profile, technical competitiveness, and process cost reduction.
High energy savings achievable with Oxsilan: It is an ambient temperature process, meaning that bath heating is usually not required at process temperatures ranging between 25 and 30°C (77 and 86°F). Consequently, a substantial reduction in energy usage can be attained resulting in considerable cost savings and reduced sensitivity to future price fluctuations in the energy markets.
Increased productivity enabled by fewer process steps: Compared to zinc-phosphating, the Oxsilan process does not require activation and passivation. The fewer process stages result in less product consumption. Additionally, the shorter treatment times, for example in the conversion coating stage, enhance productivity. (See Figure 2)
Up to 50% reduction in water consumption: The Oxsilan process requires fewer rinse stages than traditional phosphating processes. Smart rinse water management allows savings of up to 50% in water usage. Reduced water consumption also has a positive effect on the costs of waste-water and effluent treatment.